Machining method of assembly line of angular contact ball bearing sleeve ring
A technology of angular contact ball bearings and processing methods, which is applied to bearing components, shafts and bearings, mechanical equipment, etc., can solve the problems of affecting the processing accuracy of rings, low spindle accuracy life, and high manufacturing costs, so as to reduce the intensity of inspection work, The effect of reducing the number of personnel involved and reducing production costs
- Summary
- Abstract
- Description
- Claims
- Application Information
AI Technical Summary
Problems solved by technology
Method used
Image
Examples
Embodiment Construction
[0037] figure 1 It shows the flow of an embodiment of the processing method for the angular contact ball bearing ring production line of the present invention, including the outer ring connection processing process and the inner ring connection processing process,
[0038] The outer ring connection processing procedure is carried out in the following steps:
[0039] A1: Rough machining of the outer ring: rough grinding plane, rough grinding outer diameter, testing the plane and outer diameter outside the machine, if the test is unqualified, repeat the rough grinding plane and / or rough grinding outer diameter, if the test is qualified, use the grinding wheel shaft to tilt Roughly grind the groove at the angle, then grind the inner diameter and chamfer, and proceed to the next step after stabilization treatment;
[0040] A2: Fine processing of the outer ring: finely grind the plane, finely grind the outer diameter, and test the plane and outer diameter outside the machine. If t...
PUM
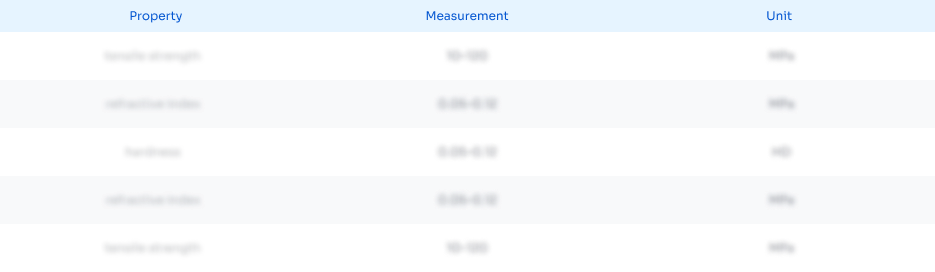
Abstract
Description
Claims
Application Information

- R&D
- Intellectual Property
- Life Sciences
- Materials
- Tech Scout
- Unparalleled Data Quality
- Higher Quality Content
- 60% Fewer Hallucinations
Browse by: Latest US Patents, China's latest patents, Technical Efficacy Thesaurus, Application Domain, Technology Topic, Popular Technical Reports.
© 2025 PatSnap. All rights reserved.Legal|Privacy policy|Modern Slavery Act Transparency Statement|Sitemap|About US| Contact US: help@patsnap.com