Catalyst for synthesis of low carbon olefins and its preparation method
A low-carbon olefin and catalyst technology, applied in the field of iron-based catalysts and their preparation, can solve the problems of easy overheating, difficult overheating, and easy deactivation of catalysts
- Summary
- Abstract
- Description
- Claims
- Application Information
AI Technical Summary
Problems solved by technology
Method used
Image
Examples
Embodiment 1
[0021] Get 606.03g of ferric nitrate nonahydrate and dissolve it in water to make solution I; dissolve 1.96g of barium nitrate and 218.3g of cobalt nitrate hexahydrate in water to make a solution, then co-flow the solution with 450g of 6% by weight ammonia solution , filtered the precipitate, and washed repeatedly with deionized water to obtain fresh and clean mixed oxide II of barium oxide and cobalt oxide, mixed solution I and mixed oxide II to obtain slurry III; SiO 2 The sol, 0.084g potassium hydroxide and 0.098g 15% by weight dilute sulfuric acid were added to slurry III, mixed and beaten, and the pH value of the slurry was adjusted to 5 with ammonia water to obtain slurry IV (solid content 15wt%). The material is spray-dried and formed, the inlet temperature of the sprayer is 380°C, the outlet temperature is 230°C, and then roasted at a roasting temperature of 750°C and a roasting time of 6 hours to obtain an iron-based Fischer-Tropsch synthesis catalyst for a microspher...
Embodiment 2
[0025]Get 606.03g iron nitrate nonahydrate and dissolve in water to make solution I; 784g barium nitrate and 2.18g cobalt nitrate hexahydrate are dissolved in water to make solution, then the solution and 1800g of 6% by weight ammonia solution are co-currently precipitated, The precipitate was filtered and washed repeatedly with deionized water to obtain fresh and clean mixed oxide II of barium oxide and cobalt oxide, and the solution I was mixed with the mixed oxide II to obtain slurry III; 3412.6 g of 40% by weight SiO 2 The sol, 6.0g sodium hydroxide and 19.6g 15% by weight dilute phosphoric acid were added to the slurry III, mixed and beaten, and the pH value of the slurry was adjusted to 1 with dilute nitric acid at the same time to obtain slurry IV (solid content: 45wt%). The slurry is spray-dried and shaped, the inlet temperature of the sprayer is 200°C, the outlet temperature is 100°C, and then roasted at a roasting temperature of 400°C and a roasting time of 0.15h to ...
Embodiment 3
[0029] Get 606.03g iron nitrate nonahydrate and dissolve in water to make solution I; 686g barium nitrate and 3.49g nickel nitrate hexahydrate are dissolved in water to make solution, then the solution and 1550g of 6% by weight ammonia solution are co-currently precipitated, The precipitate was filtered and washed repeatedly with deionized water to obtain fresh and clean mixed oxide II of barium oxide and nickel oxide, and the solution I was mixed with the mixed oxide II to obtain slurry III; 472.87g of 20% by weight TiO2 sol, 13.8g rubidium hydroxide and 17.2g 15% by weight dilute phosphoric acid were added to slurry III, mixed and beaten, and the pH value of the slurry was adjusted to 2.3 with dilute nitric acid at the same time to obtain slurry IV (solid content 35wt%). The slurry is spray-dried and molded, the inlet temperature of the sprayer is 300°C, and the outlet temperature is 180°C, and then roasted at a roasting temperature of 450°C and a roasting time of 0.5h to obt...
PUM
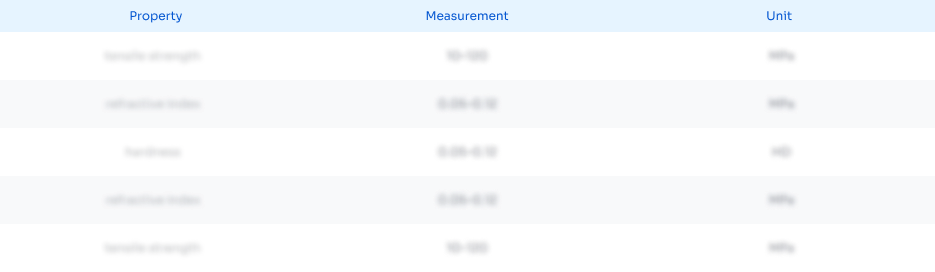
Abstract
Description
Claims
Application Information

- R&D
- Intellectual Property
- Life Sciences
- Materials
- Tech Scout
- Unparalleled Data Quality
- Higher Quality Content
- 60% Fewer Hallucinations
Browse by: Latest US Patents, China's latest patents, Technical Efficacy Thesaurus, Application Domain, Technology Topic, Popular Technical Reports.
© 2025 PatSnap. All rights reserved.Legal|Privacy policy|Modern Slavery Act Transparency Statement|Sitemap|About US| Contact US: help@patsnap.com