Preparation method of constant-hydrophilic graft-modified chlorinated polymer micro/nano fiber film
A technology of grafting modification and nanofibers, which can be used in fiber processing, textiles, papermaking, non-woven fabrics, etc., and can solve problems such as difficult grafting reactions
- Summary
- Abstract
- Description
- Claims
- Application Information
AI Technical Summary
Problems solved by technology
Method used
Image
Examples
Embodiment 1
[0023] 1. PVC dehydrochlorination treatment
[0024] Add 15.00g of SG7 type PVC resin and 10wt% NaOH solution of 10 times the mass (150.00g) into a 250mL three-necked bottle, set up a reflux device, heat to the set temperature (102°C), boil and reflux for 2h, and cool to At room temperature, vacuum filter, wash with a large amount of distilled water until all residues are removed, then transfer the product to a jar and vacuum dry to constant weight to obtain a reddish dehydrochlorinated polyvinyl chloride resin (DPVC).
[0025] 2. Preparation of spinning solution
[0026] Weigh 1.30g of DPVC resin and dissolve it in 10.00g of THF / DMF mixed solvent, wherein the mixing mass ratio of THF and DMF is 40 / 60, place it in a rotary air bath constant temperature oscillator at 25°C for 24h, fully dissolve and mix evenly, and then ultrasonically eliminate Bubble.
[0027] 3. Preparation of DPVC nanofiber membrane by electrospinning
[0028] Use a 10mL disposable sterile syringe to abso...
Embodiment 2
[0034] 1. PVC dehydrochlorination treatment
[0035] Add 15.00g of SG7 type polyvinyl chloride (PVC) resin and 10wt% NaOH solution of 10 times the mass (150.00g) into a 250mL three-necked bottle, set up a reflux device, heat to the set temperature (102°C), boil and reflux for 2h, After the reaction, cool to room temperature, vacuum filter, wash with a large amount of distilled water until all residues are removed, then transfer the product to a jar and vacuum dry to constant weight to obtain reddish DPVC.
[0036] 2. Preparation of spinning solution
[0037] Weigh 1.30g of DPVC resin and dissolve it in 10.00g of THF / DMF mixed solvent, wherein the mixing mass ratio of THF and DMF is 50 / 50, place it in a rotary air bath constant temperature shaker at 25°C for 24h, fully dissolve and mix evenly, and then sonicate defoaming.
[0038] 3. Preparation of DPVC nanofiber membrane by electrospinning
[0039] Use a 10mL disposable sterile syringe to absorb the above prepared spinning ...
Embodiment 3
[0045] 1. PVC dehydrochlorination treatment
[0046] Add 15.00g of SG7 type PVC resin and 10wt% NaOH solution of 10 times the mass (150.00g) into a 250mL three-necked bottle, set up a reflux device, heat to the set temperature (102°C), boil and reflux for 2h, and cool to At room temperature, vacuum filter, wash with a large amount of distilled water until all residues are removed, then transfer the product to a jar and vacuum dry to constant weight to obtain reddish DPVC.
[0047] 2. Preparation of spinning solution
[0048] Weigh 1.30g of DPVC resin and dissolve it in 10.00g of THF / DMF mixed solvent, wherein the mixing mass ratio of THF and DMF is 60 / 40, place it in a rotary air bath constant temperature shaker at 25°C for 24h, fully dissolve and mix evenly, and then ultrasonically eliminate Bubble.
[0049] 3. Preparation of DPVC nanofiber membrane by electrospinning
[0050] Use a 10mL disposable sterile syringe to absorb the above prepared spinning solution, clamp it on...
PUM
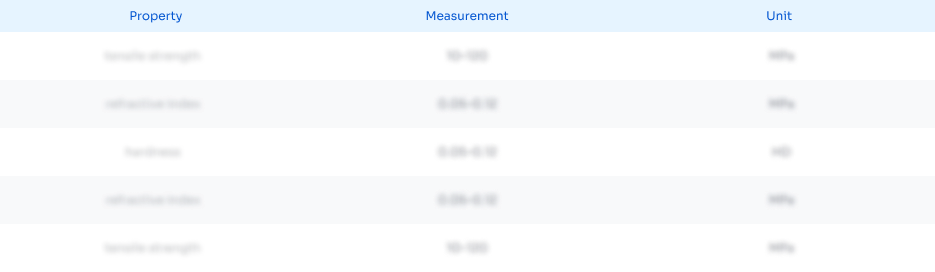
Abstract
Description
Claims
Application Information

- R&D Engineer
- R&D Manager
- IP Professional
- Industry Leading Data Capabilities
- Powerful AI technology
- Patent DNA Extraction
Browse by: Latest US Patents, China's latest patents, Technical Efficacy Thesaurus, Application Domain, Technology Topic, Popular Technical Reports.
© 2024 PatSnap. All rights reserved.Legal|Privacy policy|Modern Slavery Act Transparency Statement|Sitemap|About US| Contact US: help@patsnap.com