Full-degradation cushion packaging material and preparing method thereof
A buffer packaging and fully degradable technology, applied in the field of fully degradable buffer packaging materials and their preparation, can solve the problems of high waste pollution, non-degradation, poor environmental protection performance, etc., and achieve the effects of reliable degradation, sufficient sources and good strength
- Summary
- Abstract
- Description
- Claims
- Application Information
AI Technical Summary
Problems solved by technology
Method used
Image
Examples
Embodiment 1
[0027] (1) Weigh 50 kilograms of starch, 30 kilograms of straw, 5 kilograms of talc, 15 kilograms of glycerin, 5 kilograms of urea, 5 kilograms of polyvinyl alcohol, 0.1 kilogram of stearic acid, 1 kilogram of foaming agent AC, and 100 kilograms of water; After drying and crushing, make straw fiber segments with a length of 2 cm and an aspect ratio of about 50, then mix the starch and the treated straw fibers evenly, add glycerin, urea and 80 kg of hot water at 80°C, and stir evenly;
[0028] (2) Add talcum powder, polyvinyl alcohol, stearic acid, foaming agent AC and 20 kilograms of water, and stir evenly at 80° C. to obtain a homogeneous slurry;
[0029] (3) Add the homogeneous slurry prepared in step (2) into the mold, set the temperature of the upper mold to 180°C, the temperature of the lower mold to 195°C, and the pressure to 3Mpa, hold the pressure for 30s after closing the mold, and hold the pressure for 45s ;
[0030] (4) Demoulding, taking out the finished product t...
Embodiment 2
[0032] (1) Weigh 60 kg of starch, 20 kg of corn stalks, 10 kg of talcum powder, 10 kg of formamide, 10 kg of urea, 1 kg of polyvinyl alcohol, 1 kg of stearic acid, 0.1 kg of sodium bicarbonate, and 120 kg of water; After drying and crushing the corn stalks, cut them into 4cm-long corn stalk fiber segments with an aspect ratio of about 60, then mix the starch and the treated corn stalk fibers evenly, add formamide, urea and 100 kg of 80°C heat water, stir well;
[0033] (2) Add talcum powder, polyvinyl alcohol, stearic acid, sodium bicarbonate and 20 kilograms of water, and stir evenly at 80° C. to obtain a homogeneous slurry;
[0034] (3) Add the homogeneous slurry prepared in step (2) into the mold, set the temperature of the upper mold to 185°C, the temperature of the lower mold to 200°C, and the pressure to 2Mpa, hold the pressure for 40s after closing the mold, and hold the pressure for 60s ;
[0035] (4) Demoulding, taking out the finished product to obtain the finished...
Embodiment 3
[0037] (1) Weigh 55 kg of starch, 25 kg of wheat straw, 8 kg of talcum powder, 12 kg of glycerin, 7 kg of ethylene glycol, 3 kg of polyvinyl alcohol, 0.5 kg of stearic acid, 0.5 kg of ammonium bicarbonate, and 140 kg of water The wheat straw is dried and pulverized to make a wheat straw fiber section with a length of 3 cm and an aspect ratio of about 40, then the starch and the treated wheat straw fiber are mixed evenly, and glycerin, ethylene glycol and 120 kilograms of 80 ℃ hot water, stir evenly;
[0038] (2) Add talcum powder, polyvinyl alcohol, stearic acid, ammonium bicarbonate and water, and stir evenly at 80° C. to obtain a homogeneous slurry;
[0039] (3) Add the homogeneous slurry prepared in step (2) into the mold, set the temperature of the upper mold to 175°C, the temperature of the lower mold to 190°C, and the pressure to 3Mpa, hold the pressure for 30s after closing the mold, and dry for 30s under pressure ;
[0040] (4) Demoulding, taking out the finished pro...
PUM
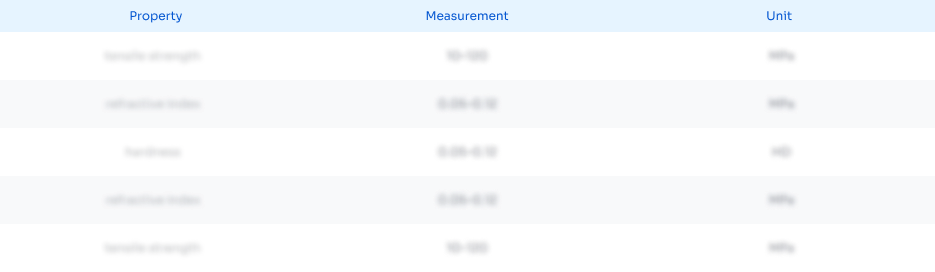
Abstract
Description
Claims
Application Information

- R&D
- Intellectual Property
- Life Sciences
- Materials
- Tech Scout
- Unparalleled Data Quality
- Higher Quality Content
- 60% Fewer Hallucinations
Browse by: Latest US Patents, China's latest patents, Technical Efficacy Thesaurus, Application Domain, Technology Topic, Popular Technical Reports.
© 2025 PatSnap. All rights reserved.Legal|Privacy policy|Modern Slavery Act Transparency Statement|Sitemap|About US| Contact US: help@patsnap.com