Preparation method of catalyst for alkane oxidation
A technology of oxygen catalyst and catalyst, which is applied in the direction of catalyst activation/preparation, preparation of organic compounds, physical/chemical process catalysts, etc. It can solve the problems of unfavorable large-scale production, high production cost, complicated methods, etc., and achieve selectivity and easy control , low production cost, good selectivity
- Summary
- Abstract
- Description
- Claims
- Application Information
AI Technical Summary
Problems solved by technology
Method used
Examples
Embodiment 1
[0020] Embodiment 1: synthesize catalyst by the inventive method
[0021] 1. Use a 3000-liter 316L stainless steel reactor, put 1500 kg of water into the reactor, and add 150 kg of ammonium vanadate. Stir and heat up to 100°C, the water boils and refluxes, and slowly add 200 kg of phosphoric acid with a concentration of 75%. The feed rate is controlled by moderate reflux of water. After the addition of phosphoric acid, continue to react for at least 4 hours under the condition of water reflux, cool down to normal temperature, centrifugally filter, and dry the filter cake at 80-100°C to obtain 300 kg of ammonium phosphovanadium powder.
[0022] 2. Configure 10% ammonium molybdate aqueous solution, put 1800 kg of water and 200 kg of ammonium molybdate into a 3000 liter enamel reaction kettle. Stir at room temperature for 1 hour, and put into buckets for later use.
[0023] 3. Weigh 300 kg of ammonium vanadium phosphate powder and add it to the silo with solid material auger s...
Embodiment 2
[0028] Synthesis of acetic acid prepared by oxidation of ethane with the catalyst of the invention.
[0029] Take 400 grams of catalyst and fill it into a single-tube reactor with molten salt control, and the catalyst layer is about 5 meters high. The air feed was 20 liters per minute and the ethane feed was 300 ml per minute. When the molten salt temperature is controlled at 390°C, the reaction bed temperature is at 445°C. Product water absorbs. The product gas chromatographic analysis shows that the acetic acid content is more than 95%, and the product contains about 3% acetaldehyde.
[0030] time Middle temperature control / ℃ Hot spot temperature / ℃ Air flowL / min Ethane flow mL / min Ethane inlet volume concentration Ethane outlet volume concentration Conversion rate CO% CO2% selectivity 9:30 412 285.6 20.0 300 1.646% 10:10 410 461.5 20.0 300 1.652% 0.38...
Embodiment 3
[0032] Synthesis of acrylic acid prepared by oxidation of propane with the catalyst of the present invention.
[0033] Take 400 grams of catalyst and fill it into a single-tube reactor with molten salt control, and the catalyst layer is about 5 meters high. The air feed was 20 liters per minute and the ethane feed was 300 ml per minute. When the molten salt temperature is controlled at 380°C, the reaction bed temperature is at 440°C. Product water absorbs. The content of acrylic acid in the product reaches 90%, the content of acetic acid is about 10%, and the content of propionic acid is about 8%.
[0034] time Middle temperature control / ℃ Hot spot temperature / ℃ Air flowL / min Propane flow mL / min Propane inlet volume concentration Propane outlet volume concentration Conversion rate CO% CO2% selectivity 9:30 407 285.6 20.0 300 1.851% 10:00 401 449.7 20.0 300 ...
PUM
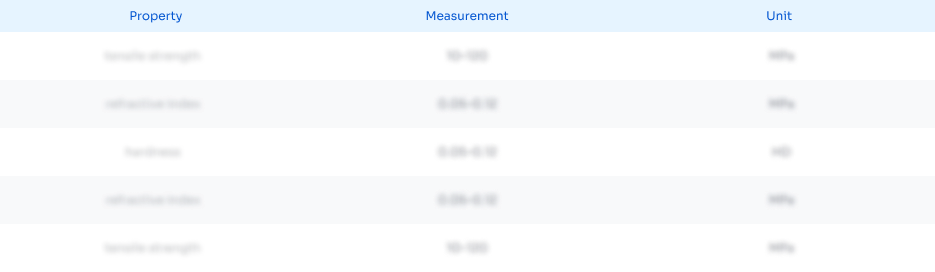
Abstract
Description
Claims
Application Information

- Generate Ideas
- Intellectual Property
- Life Sciences
- Materials
- Tech Scout
- Unparalleled Data Quality
- Higher Quality Content
- 60% Fewer Hallucinations
Browse by: Latest US Patents, China's latest patents, Technical Efficacy Thesaurus, Application Domain, Technology Topic, Popular Technical Reports.
© 2025 PatSnap. All rights reserved.Legal|Privacy policy|Modern Slavery Act Transparency Statement|Sitemap|About US| Contact US: help@patsnap.com