Burdening optimization method for sintering
An optimization method and chemical composition technology, applied in the field of sintering batching optimization, can solve problems such as the impact of blast furnace output, and achieve the effect of improving metallurgical performance and increasing economic benefits
- Summary
- Abstract
- Description
- Claims
- Application Information
AI Technical Summary
Problems solved by technology
Method used
Image
Examples
Embodiment 1
[0031] A method for optimizing sintering ingredients, characterized in that it comprises the following steps:
[0032] 1) The iron ore powder components in the mixed ore are made of Indian powder, 61 Australian powder, rolled steel sheet, iron concentrate powder, rich ore powder, Guozhong powder, roasted powder and converter slag. The above iron ore powder components are arranged in order, India The powder is the first type of iron ore powder, the 61 Australian powder is the second type of iron ore powder...the converter slag is the eighth type of iron ore powder. Dolomite, limestone, quicklime and coking coal powder are used as components to adjust the alkalinity and carbon content of the mixed ore.
[0033] 2) Determine the content percentage of chemical components in various raw materials, see Table 1. It includes determining the content percentage of 6 kinds of chemical components in various iron ore powders, and the 6 kinds of chemical components are TFe, S, Pb, Zn, K 2...
Embodiment 2
[0059] A method for optimizing sintering ingredients, characterized in that it comprises the following steps:
[0060] 1) Use 58 Australian powder, Iranian powder, Indian powder, iron concentrate powder, rich ore powder, roasting powder, Guozhong powder, and converter slag as the iron ore powder components in the mixed ore, and the above iron ore powder components are arranged in order, 58 Australian powder is the first type of iron ore powder, Iranian powder is the second type of iron ore powder... converter slag is the eighth type of iron ore powder. Dolomite, limestone, quicklime and coking coal powder are used as components to adjust the alkalinity and carbon content of the mixed ore.
[0061] 2) Determine the content percentage of chemical components in various raw materials, see Table 5. It includes determining the content percentage of 6 kinds of chemical components in various iron ore powders, and the 6 kinds of chemical components are TFe, S, Pb, Zn, K 2 O and Na 2...
PUM
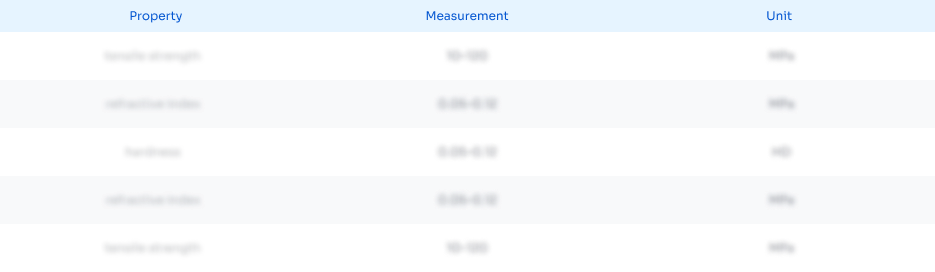
Abstract
Description
Claims
Application Information

- Generate Ideas
- Intellectual Property
- Life Sciences
- Materials
- Tech Scout
- Unparalleled Data Quality
- Higher Quality Content
- 60% Fewer Hallucinations
Browse by: Latest US Patents, China's latest patents, Technical Efficacy Thesaurus, Application Domain, Technology Topic, Popular Technical Reports.
© 2025 PatSnap. All rights reserved.Legal|Privacy policy|Modern Slavery Act Transparency Statement|Sitemap|About US| Contact US: help@patsnap.com