Method and system for reducing reduction degradation of vanadium-titanium magnet pellets
A technology of vanadium-titanium magnetite and vanadium-titanium magnet, which is applied in the field of metallurgical pellet production of vanadium-titanium magnetite, can solve problems such as failure to take preventive measures, failure to prevent pulverization, and reduction of sinter strength, etc., to achieve improvement Improvement of mechanical and kinetic properties, metallurgical performance indicators, and reduction of pulverization rate
- Summary
- Abstract
- Description
- Claims
- Application Information
AI Technical Summary
Problems solved by technology
Method used
Image
Examples
Embodiment 1
[0044] (1) Grinding vanadium-titanium magnetite to obtain vanadium-titanium magnetite powder, the ratio of which the particle size is required to be less than 0.074mm is between 60% and 80%;
[0045] (2) mixing the vanadium-titanium-magnetite powder and bentonite to obtain a mixture; the specific proportioning is, vanadium-titanium-magnetite powder 95kg, bentonite 5kg;
[0046] (3) The mixture is made into green balls on a pelletizing machine (disc pelletizing machine), and the green balls are balls with a diameter of 10-18mm; wherein, boric acid aqueous solution is added during the pelletizing process as pelletizing pellets Water, the concentration of boric acid aqueous solution is 0.1% (mass percentage); In the water tank, the boric acid aqueous solution is evenly added to the green balls during the growth process of the green balls. Based on the total mass of vanadium-titanium magnetite and bentonite as 100%, the addition amount of boric acid aqueous solution is 1%.
[00...
Embodiment 2
[0050] (1) Grinding vanadium-titanium magnetite to obtain vanadium-titanium magnetite powder, the ratio of which the particle size is required to be less than 0.074mm is between 60% and 80%;
[0051] (2) mixing the vanadium-titanium-magnetite powder and bentonite to obtain a mixture; the specific proportioning is, vanadium-titanium-magnetite powder 99kg, bentonite 1kg;
[0052] (3) The mixture is made into green balls on a pelletizing machine (cylindrical pelletizing machine), and the green balls are balls with a diameter of 10-18mm; wherein, boric acid aqueous solution is added during the pelletizing process as pelletizing pellets Water, the concentration of boric acid aqueous solution is 0.25% (mass percentage); In the water tank, the boric acid aqueous solution is evenly added to the green balls during the growth process of the green balls. Based on the mass of vanadium-titanium magnetite and bentonite as 100%, the addition amount of boric acid aqueous solution is 2%.
[...
Embodiment 3
[0056] (1) Grinding vanadium-titanium magnetite to obtain vanadium-titanium magnetite powder, the ratio of which the particle size is required to be less than 0.074mm is between 60% and 80%;
[0057] (2) mixing the vanadium-titanium-magnetite powder and bentonite to obtain a compound; the specific proportioning is, vanadium-titanium-magnetite powder 97kg, bentonite 3kg;
[0058] (3) The mixture is made into green balls on a pelletizing machine (cylindrical pelletizing machine), and the green balls are balls with a diameter of 10-18mm; wherein, boric acid aqueous solution is added during the pelletizing process as pelletizing pellets With water, the concentration of boric acid aqueous solution is 0.5% (mass percentage); the addition point of boric acid is the water addition point of the pelletizer, and boric acid and water are first prepared into a boric acid aqueous solution of the required concentration, and then added to the water tank of the pelletizer In the process of gro...
PUM
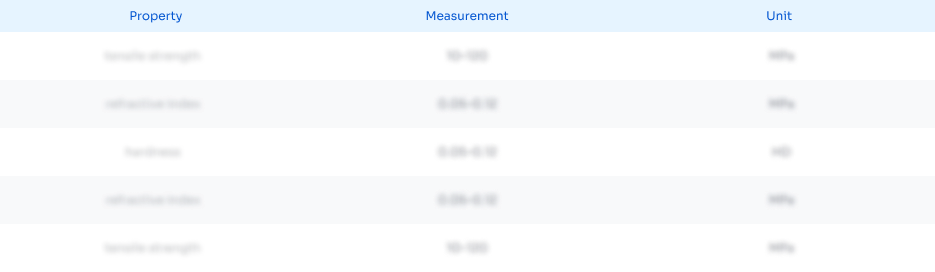
Abstract
Description
Claims
Application Information

- R&D Engineer
- R&D Manager
- IP Professional
- Industry Leading Data Capabilities
- Powerful AI technology
- Patent DNA Extraction
Browse by: Latest US Patents, China's latest patents, Technical Efficacy Thesaurus, Application Domain, Technology Topic, Popular Technical Reports.
© 2024 PatSnap. All rights reserved.Legal|Privacy policy|Modern Slavery Act Transparency Statement|Sitemap|About US| Contact US: help@patsnap.com