Bottom-blowing flow dynamic control method of top-bottom combined blowing converter
A top-bottom blowing, flow dynamic technology, applied in steel manufacturing process, manufacturing converter, process efficiency improvement and other directions, can solve problems such as inability to adjust, switching timing is advanced or delayed, affecting bottom blowing effect, etc., to achieve improvement Metallurgical effect, reducing carbon and oxygen accumulation, improving quality effect
- Summary
- Abstract
- Description
- Claims
- Application Information
AI Technical Summary
Problems solved by technology
Method used
Image
Examples
Embodiment 1
[0110] Nitrogen and argon switching mode + medium flow series, and the average value of the converter end point of the first 10 furnaces measured by the sub-lance: [C] content: 0.082wt%, [O] content: 310ppm, molten pool liquid level 892cm, temperature T = 1651℃ and the furnace age of the next furnace to be blown is 9865 furnaces; the variable parameters are brought into formula (2), and the actual injection value of the bottom blowing instantaneous flow in 8 time intervals of present embodiment 1 is calculated, see for details Table 1 below:
[0111] Table 1 The actual injection value of the instantaneous flow rate of the bottom blowing in the 8 time intervals under the nitrogen and argon switching mode + medium flow series
[0112] group F 中1
Embodiment 2
[0114] Nitrogen and argon switching mode + high flow series, and the average value of the converter end points of the first 10 furnaces measured by the sub-lance: [C] content: 0.091wt%, [O] content: 276ppm, molten pool liquid level: 880cm, temperature T = 1645 ℃; and the furnace age of the next furnace to be blown is 9868 furnaces; the variable parameters are brought into the formula (3), and the actual injection value of the bottom blowing instantaneous flow rate in the 8 time intervals of this embodiment 2 is calculated. See Table 2 below:
[0115] Table 2 The actual injection value of the instantaneous flow rate of the bottom blowing in the 8 time intervals under the nitrogen and argon switching mode + high flow series
[0116] group F 高1
Embodiment 3
[0118] Full argon blowing mode + low flow series, and the average value of the converter end point of the first 10 furnaces measured by the sub-lance: [C] content: 0.062wt%, [O] content: 412ppm, molten pool liquid level: 876cm, temperature T = 1639 ℃; and the furnace age of the next furnace to be blown is 9870 furnaces; the variable parameters are brought into the formula (1), and the actual injection value of the bottom blowing instantaneous flow rate in the 8 time intervals of this embodiment 3 is calculated. See Table 3 below:
[0119] Table 3 The actual injection value of the instantaneous flow rate of the bottom blowing in the 8 time intervals under the full argon blowing mode + low flow series
[0120] group F 低1
[0121] The methods and devices not described in detail in the present invention are all prior art and will not be repeated here.
PUM
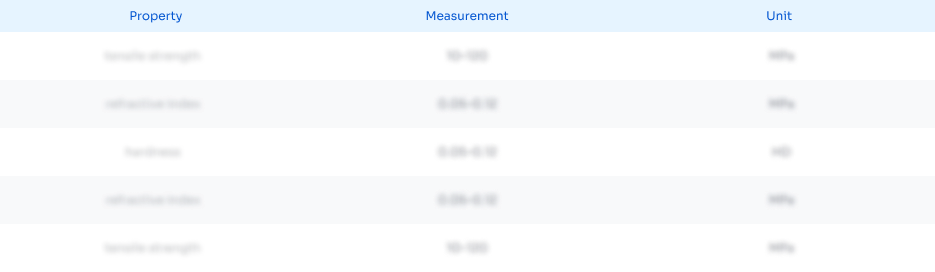
Abstract
Description
Claims
Application Information

- R&D
- Intellectual Property
- Life Sciences
- Materials
- Tech Scout
- Unparalleled Data Quality
- Higher Quality Content
- 60% Fewer Hallucinations
Browse by: Latest US Patents, China's latest patents, Technical Efficacy Thesaurus, Application Domain, Technology Topic, Popular Technical Reports.
© 2025 PatSnap. All rights reserved.Legal|Privacy policy|Modern Slavery Act Transparency Statement|Sitemap|About US| Contact US: help@patsnap.com