Method for preparing polystyrolsulfon acid aqueous solution through sodium p-styrenesulfonate polymerization
A technology of sodium styrene sulfonate and polystyrene sulfonic acid is applied in the field of preparing polystyrene sulfonic acid aqueous solution from an aqueous solution of sodium polystyrene sulfonate, and can solve the problem of limited production area, many process control points and low product sulfonation degree. And other issues
- Summary
- Abstract
- Description
- Claims
- Application Information
AI Technical Summary
Problems solved by technology
Method used
Examples
Embodiment 1
[0029] Preparation of initiator: Accurately weigh 5.7g of sodium persulfate and dissolve it in 100ml of deionized water, stir to fully dissolve it for use.
[0030] Feeding and polymerization: Add 20 L of deionized water into a 50 L reactor, then add 4.13 kg of sodium styrene sulfonate, and start the stirring speed at 85 rpm. Under the action of stirring, the temperature of the system was raised to 80° C., and the initiator was started to be added dropwise and completed within 1 hour. Keep the reaction temperature at 80±1°C, and the reaction time is 21 hours.
[0031] Discharging and acidification: After the reaction is completed, the system is cooled to room temperature 25°C under stirring, the discharge valve of the reactor is opened, and the material is discharged into the acidifier with a volume of 100L, and the stirring is started at a stirring speed of 40rpm, and the organic porous skeleton is added Solid acid 10kg, slowly stirred for 2 hours. Then use a 200-mesh polye...
Embodiment 2
[0034] Preparation of initiator: Accurately weigh 15g of sodium persulfate and dissolve it in 100ml of deionized water, stir to fully dissolve it for use.
[0035] Feeding and polymerization: Add 20 L of deionized water into a 50 L reactor, then add 4.13 kg of sodium styrene sulfonate, and start the stirring speed at 85 rpm. Under the action of stirring, the temperature of the system was raised to 80° C., and the initiator was started to be added dropwise and completed within 1 hour. Keep the reaction temperature at 80±1°C, and the reaction time is 8 hours.
[0036] Discharge and acidification: with embodiment 1.
[0037] The weight-average molecular weight of the product measured by polystyrene sulfonic acid standard sample viscosity comparison is 68,000.
Embodiment 3
[0039] Initiator preparation: accurately weigh 6g of azobisisopropylimidazoline and dissolve it in 100g of 1% polystyrene sulfonic acid aqueous solution, stir to fully dissolve it, and set aside.
[0040] Feeding and polymerization: Add 20 L of deionized water into a 50 L reactor, then add 4.13 kg of sodium styrene sulfonate, and start the stirring speed at 85 rpm. Under stirring, the temperature of the system was raised to 65° C., and the initiator was started to be added dropwise and completed within 1 hour. Keep the reaction temperature at 65±1°C, and the reaction time is 8 hours.
[0041] Discharge and acidification: with embodiment 1.
[0042] The weight-average molecular weight of the product measured by polystyrene sulfonic acid standard sample viscosity ratio is 200,000.
PUM
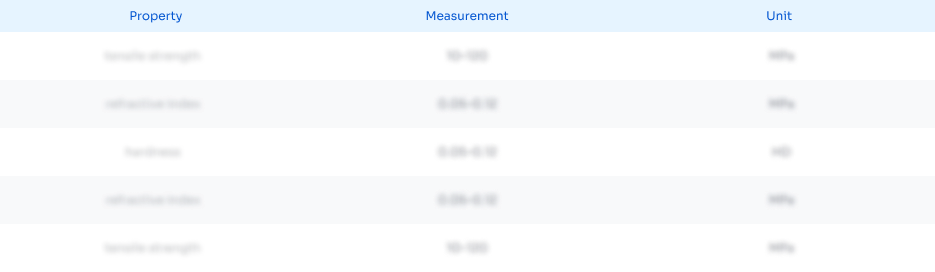
Abstract
Description
Claims
Application Information

- R&D
- Intellectual Property
- Life Sciences
- Materials
- Tech Scout
- Unparalleled Data Quality
- Higher Quality Content
- 60% Fewer Hallucinations
Browse by: Latest US Patents, China's latest patents, Technical Efficacy Thesaurus, Application Domain, Technology Topic, Popular Technical Reports.
© 2025 PatSnap. All rights reserved.Legal|Privacy policy|Modern Slavery Act Transparency Statement|Sitemap|About US| Contact US: help@patsnap.com