Method and apparatus for separation and purification of high-purity aluminum
A purification method and high-purity technology, which is applied in the field of purification of high-purity aluminum, can solve the problems of depending on the purification effect, complicated process, and large amount of consumables, and achieve the effects of expanding the source range of raw materials, improving purification efficiency, and reducing raw material costs
- Summary
- Abstract
- Description
- Claims
- Application Information
AI Technical Summary
Problems solved by technology
Method used
Image
Examples
Embodiment 1
[0029] 1) Use 27.5Kg of industrial primary aluminum with a purity of 99.7% as raw material, clean and dry its surface;
[0030] 2) Put the prepared raw materials into the smelting furnace, heat to 750°C until completely melted and then keep it warm for 1 hour;
[0031] 3) Add the refining agent intermediate alloy (aluminum-boron alloy), start the agitator to stir the reaction, let it stand for heat preservation, open the lower outlet, release the 2.5Kg aluminum liquid in the bottom layer, and transfer the 25Kg aluminum liquid in the upper layer to the segregation furnace;
[0032] 4) Segregation and crystallization, heat the segregation furnace to 660°C for 1 hour, turn on the annular gas cooling pipe, turn on the compaction device, and turn on the intermittent ultrasonic crystal stripping device. After 4 hours, stop when the aluminum liquid remains 25%, and remove the upper layer of aluminum liquid poured out;
[0033] 5) Lift the stainless steel crucible and cool it to room...
Embodiment 2
[0036] 1) Use 30Kg of industrial primary aluminum with a purity of 99.996% as raw material, clean and dry its surface;
[0037] 2) Put the prepared raw materials into the smelting furnace, heat to 680°C until completely melted, and keep warm for 1.5 hours;
[0038] 3) Add the refining agent intermediate alloy (aluminum-boron alloy), start the stirrer to stir the reaction, let it stand for heat preservation, open the lower outlet, release the 3Kg aluminum liquid in the bottom layer, and transfer the 27Kg aluminum liquid in the upper layer to the segregation furnace;
[0039] 4) Segregation crystallization, heat the segregation furnace resistance to 665°C for 2 hours, open the annular gas cooling pipe, open the compaction device, and open the intermittent ultrasonic crystal stripping device. After 4 hours, stop when the aluminum liquid remains 35%, and the upper layer of aluminum liquid poured out;
[0040] 5) Lift the stainless steel crucible and cool it to room temperature, t...
Embodiment 3
[0043] 1) Use 27.5Kg of industrial primary aluminum with a purity of 99.7% as raw material, clean and dry its surface;
[0044] 2) Put the prepared raw materials into the smelting furnace, heat to 720°C until completely melted, and then keep warm for 0.5 hours;
[0045] 3) Add the refining agent intermediate alloy (aluminum-boron alloy), start the agitator to stir the reaction, let it stand for heat preservation, open the lower outlet, release the 2.5Kg aluminum liquid in the bottom layer, and transfer the 25Kg aluminum liquid in the upper layer to the segregation furnace;
[0046] 4) Segregation and crystallization, heat the segregation furnace to 560°C for 1.5 hours, open the annular gas cooling pipe, open the compaction device, and open the intermittent ultrasonic crystal stripping device. After 4 hours, stop when the remaining 25% of the aluminum liquid, and remove the upper layer of aluminum liquid poured out,
[0047]5) Lift the stainless steel crucible and cool it to r...
PUM
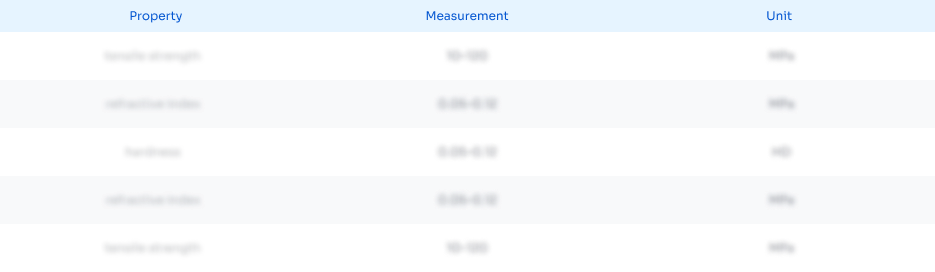
Abstract
Description
Claims
Application Information

- R&D
- Intellectual Property
- Life Sciences
- Materials
- Tech Scout
- Unparalleled Data Quality
- Higher Quality Content
- 60% Fewer Hallucinations
Browse by: Latest US Patents, China's latest patents, Technical Efficacy Thesaurus, Application Domain, Technology Topic, Popular Technical Reports.
© 2025 PatSnap. All rights reserved.Legal|Privacy policy|Modern Slavery Act Transparency Statement|Sitemap|About US| Contact US: help@patsnap.com