Preparation method of surface compound coating for guide rail of large measuring machine
A technology of surface compounding and measuring machine, which is applied in the direction of coating, metal material coating process, fusion spraying, etc., can solve the problems of unsatisfactory precision measurement, large guide rail deformation, corrosion resistance, surface condition and poor long-term reliability, etc. question
- Summary
- Abstract
- Description
- Claims
- Application Information
AI Technical Summary
Problems solved by technology
Method used
Examples
Embodiment Construction
[0016] The preparation method of the composite coating on the guide rail surface of the large measuring machine of the present invention comprises the following steps:
[0017] Step 1. Pretreatment of the surface to be sprayed of the guide rail. Visually inspect the surface to be sprayed to ensure that there are no pits, pores, and gaps. Perform coloring inspection to ensure that there are no cracks. Use acetone to wipe the surface to be sprayed to remove grease. The rounded corners on both sides are fixed with a pressure plate to protect the non-painted surface and screw holes of the guide rail;
[0018] Step 2: Carry out sand blasting roughening treatment on the surface of the guide rail to be sprayed, so that the surface of the purified substrate forms a uniform uneven rough surface, and control the roughness to the required level to ensure a good combination of the coating and the substrate;
[0019] Step 3. Using the supersonic flame spraying process, combined with the sp...
PUM
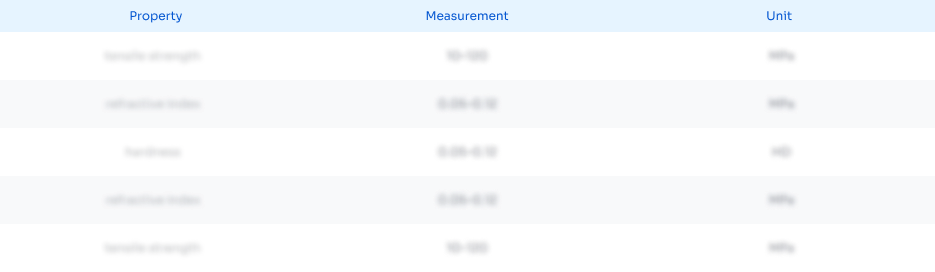
Abstract
Description
Claims
Application Information

- Generate Ideas
- Intellectual Property
- Life Sciences
- Materials
- Tech Scout
- Unparalleled Data Quality
- Higher Quality Content
- 60% Fewer Hallucinations
Browse by: Latest US Patents, China's latest patents, Technical Efficacy Thesaurus, Application Domain, Technology Topic, Popular Technical Reports.
© 2025 PatSnap. All rights reserved.Legal|Privacy policy|Modern Slavery Act Transparency Statement|Sitemap|About US| Contact US: help@patsnap.com