Chemical mechanical grinding method applied to FinFET (fin field-effect transistor) structure
A chemical-mechanical and grinding method technology, applied in electrical components, semiconductor/solid-state device manufacturing, circuits, etc., can solve problems such as nitride removal defects, and achieve the effect of simple and easy method.
- Summary
- Abstract
- Description
- Claims
- Application Information
AI Technical Summary
Problems solved by technology
Method used
Image
Examples
Embodiment Construction
[0030] The invention provides a chemical mechanical polishing method applied to a FINFET structure, which uses a CMP process and adds an endpoint detection method, so that the grinding can completely remove silicon nitride and stop on the oxide layer of the buffer pad, so as to completely remove nitrogen by using the CMP process For the purpose of silicon nitride, there is no need for wet removal of silicon nitride. This endpoint detection method is to use the change of motor torque current caused by the change of wafer surface friction before and after silicon nitride removal, so as to collect the torque current signal and capture the sudden change that stops on the buffer oxide layer after grinding and removing silicon nitride. Signal point to achieve the effect of grinding stop.
[0031] The method of the present invention will be described in detail below in conjunction with the accompanying drawings.
[0032] A chemical mechanical polishing method applied to a FINFET str...
PUM
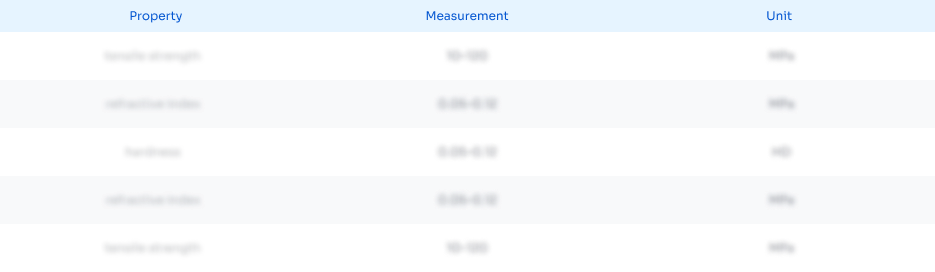
Abstract
Description
Claims
Application Information

- R&D
- Intellectual Property
- Life Sciences
- Materials
- Tech Scout
- Unparalleled Data Quality
- Higher Quality Content
- 60% Fewer Hallucinations
Browse by: Latest US Patents, China's latest patents, Technical Efficacy Thesaurus, Application Domain, Technology Topic, Popular Technical Reports.
© 2025 PatSnap. All rights reserved.Legal|Privacy policy|Modern Slavery Act Transparency Statement|Sitemap|About US| Contact US: help@patsnap.com