Temperature-resistant macromolecule self-seal rubber and manufacturing method thereof
A manufacturing method and polymer technology, applied in coatings, rosin coatings, etc., to achieve superior elasticity and ductility, prevent leakage, and improve driving safety
- Summary
- Abstract
- Description
- Claims
- Application Information
AI Technical Summary
Problems solved by technology
Method used
Examples
Embodiment 1
[0046] Proportion and components of heat-resistant polymer self-sealing adhesive (based on mass percent): 100 thermoplastic elastomer, 86.5 tackifier, 11.7 plasticizer, antioxidant and anti-aging agent 3 in total, foaming agent 19; weigh Thermoplastic elastomer SIS80, thermoplastic elastomer SEBS20; tackifier: terpene resin 75, polyisobutylene 11.5; plasticizer: naphthenic oil 11, diisooctyl phthalate 0.7; antioxidant 4010A1.5, antioxidant 10761.5; Blowing agent: AC19.
[0047] The preparation method is as follows: using material crushing equipment to crush the solid material into particles of <150 mesh; using a continuous mixing equipment high-shear disperser to uniformly mix the crushed solid material and liquid material, and measure and pack the powder after mixing evenly.
Embodiment 2
[0049] Proportion and components of heat-resistant polymer self-sealing adhesive (based on mass percent): 100 thermoplastic elastomer, 75 tackifier, 6 plasticizer, 1 antioxidant, foaming agent 4; weigh thermoplastic elastomer SIS85 , thermoplastic elastomer SEBS15; tackifier: rosin glyceride 65, polyisobutylene 10; plasticizer: naphthenic oil 5.5, diisooctyl phthalate (DIOP) 0.5; antioxidant 10100.5, antioxidant 3000.5; Foaming agent: ADC4.
[0050] The preparation method is as follows: using material crushing equipment to crush the solid material into particles of <150 mesh; using a continuous mixing device planetary mixer to uniformly mix the crushed solid material and liquid material, and then measure and bag the mixture after uniform mixing.
PUM
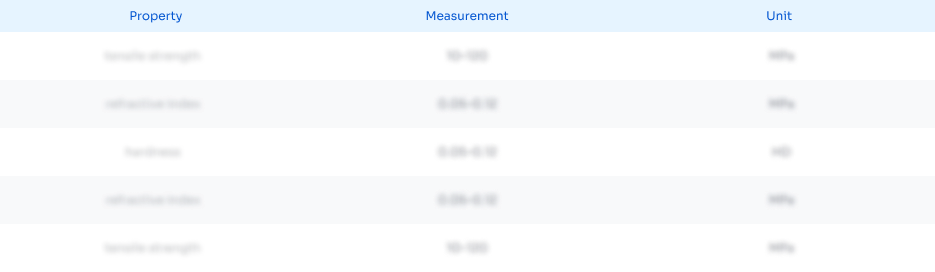
Abstract
Description
Claims
Application Information

- Generate Ideas
- Intellectual Property
- Life Sciences
- Materials
- Tech Scout
- Unparalleled Data Quality
- Higher Quality Content
- 60% Fewer Hallucinations
Browse by: Latest US Patents, China's latest patents, Technical Efficacy Thesaurus, Application Domain, Technology Topic, Popular Technical Reports.
© 2025 PatSnap. All rights reserved.Legal|Privacy policy|Modern Slavery Act Transparency Statement|Sitemap|About US| Contact US: help@patsnap.com