Synthesis process of ultrafine-grade diamond
A synthesis process and diamond technology, which is applied in the field of ultrafine diamond synthesis process, can solve the problems of no crystal shape, limited application range, and influence on mechanical properties of crystals, and achieve the effect of less impurities, consistent crystal form, and large nucleation amount
- Summary
- Abstract
- Description
- Claims
- Application Information
AI Technical Summary
Problems solved by technology
Method used
Image
Examples
Embodiment 1
[0047] Embodiment 1 Concrete synthetic steps are:
[0048] ① Take 400 mesh finer graphite powder and Fe-based alloy catalyst powder and mix them in a weight ratio of 8:5. The components and contents of the Fe-based alloy catalyst powder are calculated by weight percentage: Si: 0.5%, B: 0.2%, Cu: 6%, Zn: 3%, dispersant: 0.5%, the balance is Fe;
[0049] ②Put the raw material obtained in step ① into a three-dimensional mixer and mix for 2 hours. After isostatic pressing at 220MPa, crush it into particles smaller than 90 meshes to obtain the mixed material;
[0050] ③Put the mixed material into the mold, and then press it into a columnar stem on a four-column press. The size of the stem: Φ40mm×31.5mm, the density of the stem: 3.5g / cm 3 , put the formed core column into a vacuum furnace, vacuum treatment at 1000°C, fully remove oxygen, and cool down to room temperature naturally;
[0051] ④ Put the core column into the diamond synthesis block, and then put the diamond synthe...
Embodiment 2
[0057] Embodiment 2 Concrete synthetic steps are:
[0058] ① Take 400 mesh finer graphite powder and Fe-based alloy catalyst powder and mix them in a weight ratio of 8:7. The components and contents of the Fe-based alloy catalyst powder are calculated by weight percentage: Si: 1.7%, B: 1.4%, Cu: 7%, Zn: 7%, dispersant: 1%, the balance is Fe;
[0059] ②Put the raw material obtained in step ① into a three-dimensional mixer and mix for 2 hours. After isostatic pressing at 280MPa, crush it into particles smaller than 90 meshes to obtain the mixed material;
[0060] ③Put the mixed material into the mold, and then press it into a columnar core column on a four-column press. The size of the core column: Φ40mm×31.5mm, the density of the core column: 3.8g / cm 3 , put the formed core column into a vacuum furnace, vacuum treatment at 1000°C, fully remove oxygen, and cool down to room temperature naturally;
[0061] ④Put the core column into the diamond synthesis block, and then put ...
Embodiment 3
[0067] Embodiment 3 Concrete synthetic steps are:
[0068] ① Take 400 mesh finer graphite powder and Fe-based alloy catalyst powder and mix them in a weight ratio of 8:6. The composition and content of the Fe-based alloy catalyst powder are calculated by weight percentage: Si: 1.1%, B: 0.8%, Cu: 6.5%, Zn: 5%, dispersant: 0.75%, the balance is Fe;
[0069] ② Put the raw materials obtained in step ① into a three-dimensional mixer and mix them for 2 hours. After isostatic pressing at 250 MPa, they are crushed into particles smaller than 90 meshes to obtain the mixed materials;
[0070] ③Put the mixed material into the mold, and then press it into a columnar core column on a four-column press. The size of the core column: Φ40mm×31.5mm, the density of the core column: 3.7g / cm 3 , put the formed core column into a vacuum furnace, vacuum treatment at 1000°C, fully remove oxygen, and cool down to room temperature naturally;
[0071] ④ Put the core column into the diamond synthesis b...
PUM
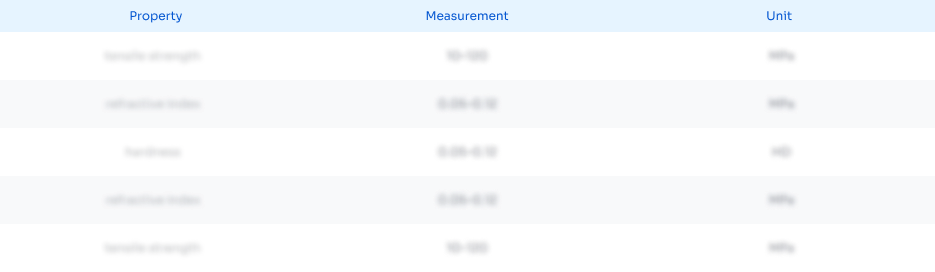
Abstract
Description
Claims
Application Information

- Generate Ideas
- Intellectual Property
- Life Sciences
- Materials
- Tech Scout
- Unparalleled Data Quality
- Higher Quality Content
- 60% Fewer Hallucinations
Browse by: Latest US Patents, China's latest patents, Technical Efficacy Thesaurus, Application Domain, Technology Topic, Popular Technical Reports.
© 2025 PatSnap. All rights reserved.Legal|Privacy policy|Modern Slavery Act Transparency Statement|Sitemap|About US| Contact US: help@patsnap.com