A kind of cerium molybdenum zirconium composite oxide catalyst, its preparation method and application
A technology of composite oxides and catalysts, applied in metal/metal oxide/metal hydroxide catalysts, physical/chemical process catalysts, chemical instruments and methods, etc., can solve low conversion rate, thermal stability and anti-sintering ability Poor, narrow temperature window and other problems, to achieve high conversion rate, excellent thermal stability and anti-sintering ability, wide temperature window effect
- Summary
- Abstract
- Description
- Claims
- Application Information
AI Technical Summary
Problems solved by technology
Method used
Image
Examples
Embodiment 1~6
[0052] A preparation method of cerium molybdenum zirconium composite oxide catalyst, comprising the steps of:
[0053] (1) Dissolve cerium nitrate and zirconium nitrate in deionized water, stir until completely dissolved, add ammonium molybdate aqueous solution, and then add water to about 250mL to obtain a precursor solution of cerium, molybdenum, and zirconium, and control cerium, molybdenum, and zirconium The concentration of cerium, molybdenum and zirconium ions in the precursor solution;
[0054] (2) Add urea to the precursor solution of cerium, molybdenum, and zirconium obtained in step (1), stir at 90°C for 12 hours to precipitate metal ions, and obtain a mixed solution; the urea and metal ions (cerium, molybdenum, and zirconium ions The sum of moles) has a molar ratio of 10;
[0055] (3) After cooling the mixed liquid obtained in step (2) to room temperature, filter the precipitate to obtain the precipitate, wash the precipitate to neutrality, then dry it in an oven a...
Embodiment 7
[0079] A preparation method of cerium molybdenum zirconium composite oxide catalyst, comprising the steps of:
[0080] (1) Dissolve the cerium precursor and zirconium precursor in deionized water, stir until completely dissolved, then add the aqueous solution of the molybdenum precursor, and then add water to about 250mL to obtain the precursor solution of cerium, molybdenum, and zirconium, and control the cerium, molybdenum, and zirconium precursor solutions. The concentration of cerium in the precursor solution of molybdenum and zirconium is 0.06mol / L, the concentration of molybdenum is 0.06mol / L, and the concentration of zirconium is 0.12mol / L;
[0081] (2) Add urea to the precursor solution of cerium, molybdenum and zirconium obtained in step (1), stir and precipitate metal ions at 80°C to obtain a mixed solution; the precipitant and metal ions (cerium, molybdenum, zirconium ions sum) the molar ratio is 8;
[0082](3) After cooling the mixed liquid obtained in step (2) to...
Embodiment 8
[0085] A preparation method of cerium molybdenum zirconium composite oxide catalyst, comprising the steps of:
[0086] (1) Dissolve the cerium precursor and the zirconium precursor in deionized water, stir until completely dissolved, then add the aqueous solution of the molybdenum precursor, and then add water to about 250mL to obtain the precursor solution of cerium, molybdenum, and zirconium, and control the cerium, molybdenum, and zirconium precursor solutions. The concentration of cerium in the precursor solution of molybdenum and zirconium is 0.1mol / L, the concentration of molybdenum is 0.1mol / L, and the concentration of zirconium is 0.2mol / L;
[0087] (2) Add urea to the precursor solution of cerium, molybdenum and zirconium obtained in step (1), stir and precipitate metal ions at 95°C to obtain a mixed solution; the precipitant and metal ions (cerium, molybdenum, zirconium ions and the molar ratio of 15;
[0088] (3) After cooling the mixed liquid obtained in step (2) ...
PUM
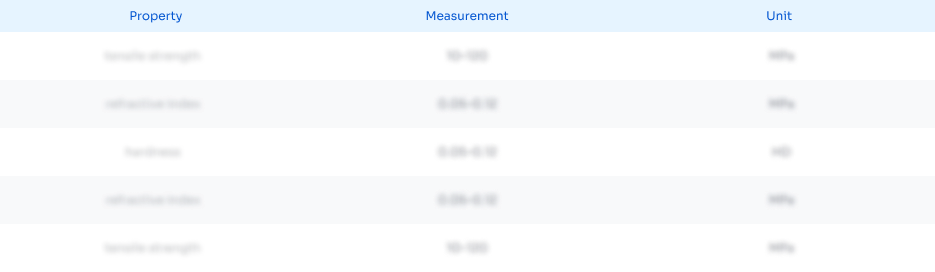
Abstract
Description
Claims
Application Information

- R&D
- Intellectual Property
- Life Sciences
- Materials
- Tech Scout
- Unparalleled Data Quality
- Higher Quality Content
- 60% Fewer Hallucinations
Browse by: Latest US Patents, China's latest patents, Technical Efficacy Thesaurus, Application Domain, Technology Topic, Popular Technical Reports.
© 2025 PatSnap. All rights reserved.Legal|Privacy policy|Modern Slavery Act Transparency Statement|Sitemap|About US| Contact US: help@patsnap.com