Injection molding zirconium oxide and preparation method for same
An injection molding, phase zirconia technology, which is applied in the field of zirconia fine ceramic materials, can solve the problems of inability to achieve rapid miscibility of the binder, difficulty in mixing powder and binder, and non-spherical shape or agglomeration. Avoid deformation, fluidity does not agglomerate, good fluidity effect
- Summary
- Abstract
- Description
- Claims
- Application Information
AI Technical Summary
Problems solved by technology
Method used
Image
Examples
Embodiment 1
[0023] The commercially available zirconia injection powder and organic carrier are mixed in a weight ratio of 100:13; after banburying, the injection molding material is obtained, and then the green body is made by injection molding process, and the secondary degreasing treatment of oil soaking and heating degreasing is carried out. Finally, a high-performance zirconia ceramic ferrule is made through a sintering process. The powder organic carrier is a mixture of EVA and polystyrene, polypropylene, vegetable oil, oleic acid, paraffin, and the powder organic carrier proportioning is as follows according to the total weight percentage of the powder organic carrier:
[0024] Paraffin: 20~90%.
[0025] Oleic acid: 0~30%
[0026] Polystyrene: 5~30%
[0027] Polypropylene: 2~40%
[0028] Stearic acid: 0~10%
[0029] Beeswax: 0~10%
[0030] The zirconia ceramic injection manufacturing process includes:
[0031] (1) Banbury
[0032] First raise the temperature of the internal ...
Embodiment 2
[0042] (1) with ZrOCl 2 ·8H 2 O, Y 2 o 3 Make a mixed aqueous solution for the raw materials, add the third component and dispersant at the same time, and the Zr in the mixed solution 4+ The ion concentration is 2mol / L; the dispersant is polyacrylic acid PAA, sodium polyacrylate PAAS, polymaleic acid, polymaleic anhydride HPMA, maleic acid-acrylic acid copolymer MA-AA, acrylic acid-2-acrylamide-2- One or more combinations of methylpropanesulfonic acid polypolymer AA / AMPS, modified polycarboxylate, polyacrylate, polyvinyl alcohol;
[0043] (2) Add precipitant ammonium oxalate to the mixed aqueous solution in step (1), the added precipitant is ammonium oxalate, and the added ratio is nZr 4+ ︰n ammonium oxalate≈1︰(1.2~1.3);
[0044](3) Then vibrating mill stirring to obtain ultra-fine, uniformly dispersed sediment;
[0045] (4) Wash the precipitate prepared in step (3) with distilled water several times to remove almost all chloride ions;
[0046] (5) Add an appropriate am...
Embodiment 3
[0070] (1) with ZrOCl 2 ·8H 2 O, Y 2 o 3 Make a mixed aqueous solution for the raw materials, add the third component and dispersant at the same time, and the Zr in the mixed solution 4+ The ion concentration is 3mol / L; the dispersant is polyacrylic acid PAA, sodium polyacrylate PAAS, polymaleic acid, polymaleic anhydride HPMA, maleic acid-acrylic acid copolymer MA-AA, acrylic acid-2-acrylamide-2- One or more combinations of methylpropanesulfonic acid polypolymer AA / AMPS, modified polycarboxylate, polyacrylate, polyvinyl alcohol;
[0071] (2) Add precipitant ammonium oxalate to the mixed aqueous solution in step (1), the added precipitant is ammonium oxalate, and the added ratio is nZr4+:n ammonium oxalate≈1:(1.2~1.3);
[0072] (3) Then vibrating mill stirring to obtain ultra-fine, uniformly dispersed sediment;
[0073] (4) Wash the precipitate prepared in step (3) with distilled water several times to remove almost all chloride ions;
[0074] (5) Add an appropriate amou...
PUM
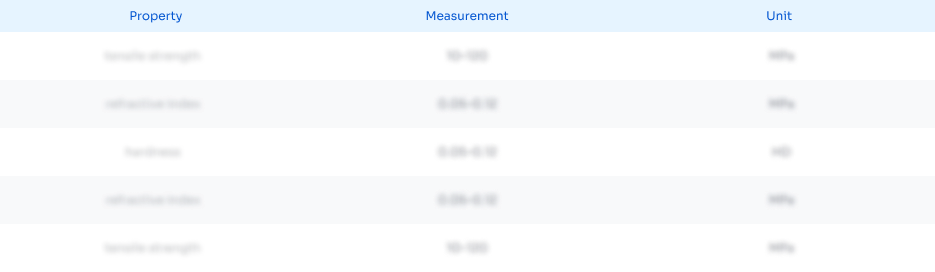
Abstract
Description
Claims
Application Information

- Generate Ideas
- Intellectual Property
- Life Sciences
- Materials
- Tech Scout
- Unparalleled Data Quality
- Higher Quality Content
- 60% Fewer Hallucinations
Browse by: Latest US Patents, China's latest patents, Technical Efficacy Thesaurus, Application Domain, Technology Topic, Popular Technical Reports.
© 2025 PatSnap. All rights reserved.Legal|Privacy policy|Modern Slavery Act Transparency Statement|Sitemap|About US| Contact US: help@patsnap.com