Water lubricated bearing with high bearing capacity and self lubricity
A water-lubricated bearing, self-lubricating technology, used in bearing cooling, bearing components, shafts and bearings, etc., can solve problems such as uneven dispersion of oil compounds, unstable bearing vibration and radial force, and impact on bearing service life. , to achieve excellent self-lubricating and wear resistance, prevent bearing seizure, and prevent noise.
- Summary
- Abstract
- Description
- Claims
- Application Information
AI Technical Summary
Problems solved by technology
Method used
Image
Examples
Embodiment 1
[0031] In a sealed reactor, heat 2000g of polytetrahydrofuran (PTMG, molecular weight 2000) polyol to 100°C with a vacuum of 0.08MPa, and carry out vacuum dehydration for 3 hours to control the water content below 0.05%. Cool the dehydrated PTMG to 60°C, then slowly add 350g of 2,4-toluene diisocyanate (TDI), stir under nitrogen atmosphere, and start to heat up to 80°C±5°C, keep the reaction for 2 hours, and carry out vacuum desorption Remove air bubbles, then add 120g of amino-terminated polydimethylsiloxane (PDMS, molecular weight 1000), stir the reaction, control the temperature of the prepolymer at 65°C, stir to remove air bubbles, and continue for about 90min; wait for the air bubbles to be removed After completion, add 130g of polytetrafluoroethylene, 50g of graphite, and 200g of glass fiber, continue stirring and vacuum to remove air bubbles, and heat 680g of 4,4'-diamino-3,3'-dichlorodiphenylmethane (MOCA) Melt it, slowly add it to the synthetic polyurethane matrix tha...
Embodiment 2
[0033] In a sealed reactor, heat 2000g of tetrahydrofuran-ethylene oxide-propylene oxide copolyether (PTMG-PO, molecular weight 2000) to 100°C, vacuum at 0.08MPa, and carry out vacuum dehydration for 3 hours to control the water content below 0.05 %. Cool the dehydrated PTMG-PO to 60°C, then slowly add 260g of 2,4-toluene diisocyanate (TDI), stir under a nitrogen atmosphere, and start to heat up to 80°C±5°C, keep the temperature for 2 hours, and carry out Remove the air bubbles in vacuum, then add 180g of hydroxyl-terminated polydimethylsiloxane (PDMS, molecular weight 1000), stir the reaction, control the temperature of the prepolymer at 65°C, start the stirring, and remove the air bubbles for about 90 minutes; After the air bubbles are completely removed, add 360g of polytetrafluoroethylene, 25g of graphite, and 30g of glass fiber, continue stirring and vacuum to remove air bubbles, and 700g of 4,4'-diamino-3,3'-dichlorodiphenylmethane ( MOCA) for heating and melting, after...
Embodiment 3
[0035] In a sealed reactor, heat 2000g of polytetrahydrofuran polyol (PTMG, molecular weight 2000) to 100°C with a vacuum of 0.08MPa, and carry out vacuum dehydration for 3 hours to control the water content below 0.05%. Cool the dehydrated PTMG to 60°C, then slowly add 260g of diphenylmethane-4,4'-diisocyanate (MDI), stir under nitrogen atmosphere, and start to heat up to 80°C ± 5°C, heat preservation reaction 2 After 1 hour, carry out vacuum to remove air bubbles, then add 180g of amino-terminated polydimethylsiloxane (PDMS, molecular weight 1000), stir the reaction, control the temperature of the prepolymer at 65°C, remove air bubbles under stirring, and last for about 90min; after the air bubbles are completely removed, add 360g polytetrafluoroethylene, 100g graphite, and 200g aramid fibers, continue to stir and remove air bubbles in a vacuum, and add 550g 2,4-diamino-3,5-dimethylthio Toluene (DMTDA) is heated and melted, slowly added, quickly stirred and mixed, immediatel...
PUM
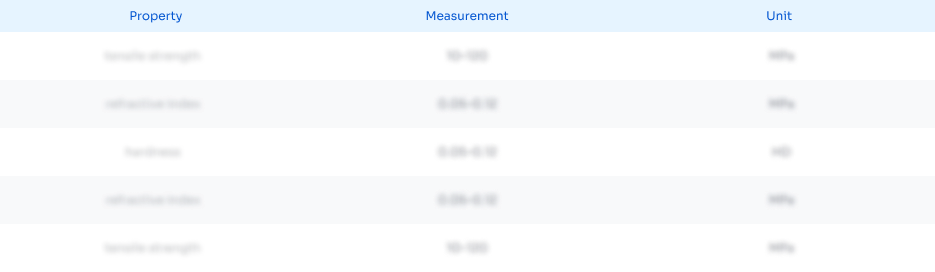
Abstract
Description
Claims
Application Information

- Generate Ideas
- Intellectual Property
- Life Sciences
- Materials
- Tech Scout
- Unparalleled Data Quality
- Higher Quality Content
- 60% Fewer Hallucinations
Browse by: Latest US Patents, China's latest patents, Technical Efficacy Thesaurus, Application Domain, Technology Topic, Popular Technical Reports.
© 2025 PatSnap. All rights reserved.Legal|Privacy policy|Modern Slavery Act Transparency Statement|Sitemap|About US| Contact US: help@patsnap.com