A kind of refining method of crude sulfate turpentine
A technology of sulfate turpentine and refining method, which is applied in chemical instruments and methods, purification/separation of hydrocarbons, hydrocarbons, etc., and can solve the problems of difficulty in obtaining ultra-low sulfur pinene products, difficulty in controlling the air oxidation process, and easy formation of terpenes Solve problems such as peroxides, and achieve the effects of strong industrial reliability, high product yield and simple method
- Summary
- Abstract
- Description
- Claims
- Application Information
AI Technical Summary
Problems solved by technology
Method used
Image
Examples
Embodiment 1
[0036] The mass composition of crude sulfate turpentine raw material is: pinene (α-pinene and β-pinene) 82%, total sulfur 1023ppm, water 0.3%, solid impurities 0.21%, and the rest are other terpenoid components.
[0037] (1) The crude sulfate turpentine raw material is preheated at 55°C by heat exchanger E-1 at a rate of 12kg / h, and then enters flash tower T-1 from pipeline 1 for flash separation treatment. The temperature in the flash tower is 102°C, the temperature of the reboiler in the packing separation section is 104°C. Light sulfur components such as sulfides and mercaptans with a boiling point lower than α-pinene flowing out from the top of the flash tower are output to the alkali neutralization absorption system R-2 through pipeline 2, and are neutralized by existing methods Direct discharge; while the initial desulfurization material (with a sulfur content of 35.4ppm) flowing out from the bottom of the flash tower is output to the vacuum rectification tower T-2 throu...
Embodiment 2
[0042] The mass composition of crude sulfate turpentine raw material is: pinene (α-pinene and β-pinene) 88%, total sulfur 897ppm, moisture 0.35%, solid impurities 0.33%, and the rest are other terpenoid components.
[0043] (1) The crude sulfate turpentine raw material is preheated to 60°C through the heat exchanger E-1 at a rate of 14kg / h, and then enters the flash tower T-1 from the pipeline 1 for flash separation treatment. The temperature in the flash tower is 101°C, and the reboiler temperature in the packing separation section is 103°C. Light sulfur components such as sulfides and mercaptans with a boiling point lower than α-pinene flowing out from the top of the flash tower are output to the alkali neutralization absorption system R-2 through pipeline 2, and are neutralized by existing methods Direct discharge; while the initial desulfurized material (with a sulfur content of 32.3ppm) flowing out from the bottom of the flash tower is output to the vacuum rectification t...
Embodiment 3
[0048] The mass composition of crude sulfate turpentine raw material is: pinene (α-pinene and β-pinene) 81%, total sulfur 623ppm, moisture 0.31%, solid impurities 0.19%, and the rest are other terpenoid components.
[0049] (1) The crude sulfate turpentine raw material is preheated to 66°C through the heat exchanger E-1 at a rate of 10kg / h, and then enters the flash tower T-1 from the pipeline 1 for flash separation treatment. The temperature in the flash tower is 105°C, and the temperature of the reboiler in the packing separation section is 107°C. Light sulfur components such as sulfides and mercaptans with a boiling point lower than α-pinene flowing out from the top of the flash tower are output to the alkali neutralization absorption system R-2 through pipeline 2, and are neutralized by existing methods Direct discharge; while the initial desulfurization material (with a sulfur content of 33.7ppm) flowing out from the bottom of the flash tower is output to the vacuum recti...
PUM
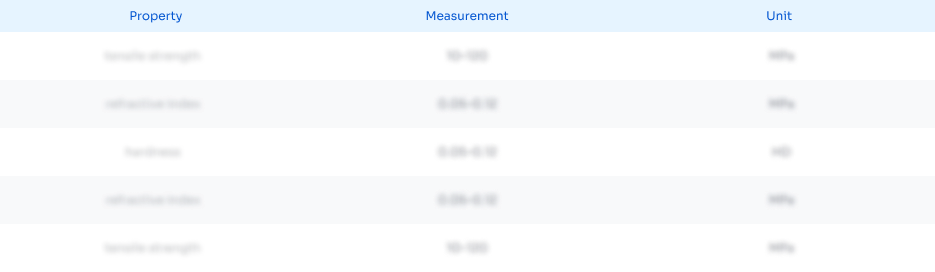
Abstract
Description
Claims
Application Information

- R&D Engineer
- R&D Manager
- IP Professional
- Industry Leading Data Capabilities
- Powerful AI technology
- Patent DNA Extraction
Browse by: Latest US Patents, China's latest patents, Technical Efficacy Thesaurus, Application Domain, Technology Topic, Popular Technical Reports.
© 2024 PatSnap. All rights reserved.Legal|Privacy policy|Modern Slavery Act Transparency Statement|Sitemap|About US| Contact US: help@patsnap.com