Chip packaging method and packaging structure
A technology of chip packaging and packaging structure, which is applied in the direction of electrical components, electrical solid devices, semiconductor/solid device manufacturing, etc., to achieve the effects of improving reliability, improving electrical connection performance, and improving interface quality
- Summary
- Abstract
- Description
- Claims
- Application Information
AI Technical Summary
Problems solved by technology
Method used
Image
Examples
Embodiment Construction
[0034] As mentioned in the background art, the reliability of the packaging structure formed by the existing chip packaging method is low.
[0035] On the one hand, because the thickness of the solder resist layer filled in the groove is relatively large, during the process of thermal curing of the solder resist layer, due to the difference in thermal expansion coefficient between the solder resist layer and the wafer, greater stress will be generated , and passed to the customer layer, generating greater stress in the customer layer; subsequent reflow soldering process is used to form solder balls, and the high temperature in the reflow soldering process will also cause stress in the customer layer. Since the client layer is a complete whole before wafer dicing, the stress in the client layer cannot be completely released. When the chip is cut, the customer layer is no longer a whole. At this time, the thermal curing of the solder mask layer, the residual stress in the solder...
PUM
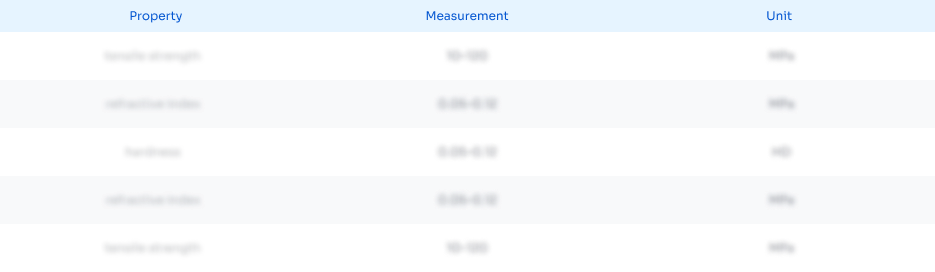
Abstract
Description
Claims
Application Information

- R&D
- Intellectual Property
- Life Sciences
- Materials
- Tech Scout
- Unparalleled Data Quality
- Higher Quality Content
- 60% Fewer Hallucinations
Browse by: Latest US Patents, China's latest patents, Technical Efficacy Thesaurus, Application Domain, Technology Topic, Popular Technical Reports.
© 2025 PatSnap. All rights reserved.Legal|Privacy policy|Modern Slavery Act Transparency Statement|Sitemap|About US| Contact US: help@patsnap.com