EPDM/polypropylene thermoplastic elastomer and preparation process thereof
A thermoplastic elastomer, EPDM technology, which is applied in the field of resource reuse of waste tires (waste EPDM), can solve the problem that it is difficult to meet the requirements of activation treatment, affect the effect of subsequent processes, and cannot achieve Activation requirements and other issues, to achieve the effect of expanding a wide range of hardness changes, excellent toughening, and improving plasticity and elasticity
- Summary
- Abstract
- Description
- Claims
- Application Information
AI Technical Summary
Problems solved by technology
Method used
Image
Examples
Embodiment 1
[0049]The material formula consists of: PP (F401), recycled PP, plasticized rubber powder, naphthenic oil, POE, 1250 mesh talc, antioxidant 1010, PE wax, butyl methacrylate, DCP; among them, plasticized rubber The powder is obtained by pretreatment of waste EPDM rubber powder (containing more than 40% of glue), and the pretreatment formula is composed of the following components in parts by weight: 80 mesh waste EPDM rubber powder, solid coal tar, rubber Activator 420, surfactant TAIC, 1250 mesh talc. See Table 1 for specific parts by weight.
[0050] Preparation process: (1) First, put the waste EPDM rubber powder into the high mixer for 1400 rpm treatment, when the temperature rises to 80 degrees, add solid coal tar, activator, surfactant, continue stirring, and wait for the rubber powder to dissolve. The temperature was raised to 150 degrees, talc was added, quenched to room temperature, and sealed for later use. (2) Then add PP raw material, POE, naphthenic oil, antioxid...
Embodiment 2
[0059] The material formula consists of: PP (F401), plasticized rubber powder, naphthenic oil, POE, 1250 mesh talc, antioxidant 1010, PE wax, butyl methacrylate, DCP, anti-ultraviolet additive UV-9; Wherein, the plasticized rubber powder is obtained from waste EPDM rubber powder (with a rubber content greater than 40%) through pretreatment, and the pretreatment formula is composed of the following components in parts by weight: 80 mesh waste EPDM rubber powder, Solid coal tar, rubber activator 450, surfactant silane coupling agent 602, 1250 mesh talc. See Table 1 for specific parts by weight.
[0060] Preparation process: (1) First, put the waste EPDM rubber powder into the high mixer for 1400 rpm treatment, when the temperature rises to 80 degrees, add solid coal tar, activator, surfactant, continue stirring, and wait for the rubber powder to dissolve. The temperature was raised to 150 degrees, talc was added, quenched to room temperature, and sealed for later use. (2) Then...
Embodiment 3
[0067] The material formula is composed of: recycled PP, plasticized rubber powder, naphthenic oil, POE, 1250 mesh talc, antioxidant 1010, PE wax, butyl methacrylate, DCP, sericite; among which, the plasticized rubber powder is composed of Waste EPDM rubber powder (containing more than 40% of glue) is obtained through pretreatment, and the pretreatment formula is composed of the following components in parts by weight: 80 mesh waste EPDM rubber powder, solid coal tar, rubber activator 480, surfactant (oleic acid), 1250 mesh talc. See Table 1 for specific parts by weight.
[0068] The preparation process is the same as that of Example 1.
[0069] Table 1 Material components, pretreatment formulations and their physical and mechanical properties used in each example
[0070]
PUM
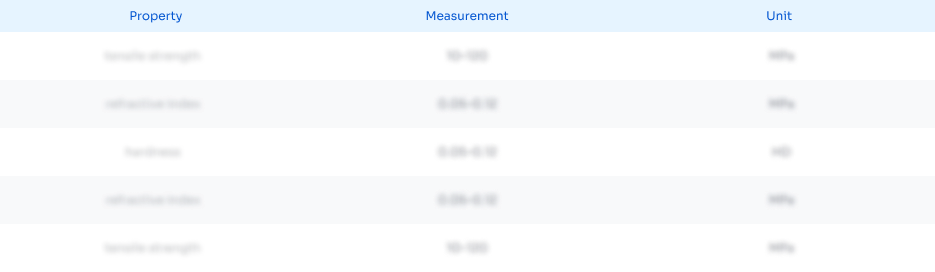
Abstract
Description
Claims
Application Information

- R&D
- Intellectual Property
- Life Sciences
- Materials
- Tech Scout
- Unparalleled Data Quality
- Higher Quality Content
- 60% Fewer Hallucinations
Browse by: Latest US Patents, China's latest patents, Technical Efficacy Thesaurus, Application Domain, Technology Topic, Popular Technical Reports.
© 2025 PatSnap. All rights reserved.Legal|Privacy policy|Modern Slavery Act Transparency Statement|Sitemap|About US| Contact US: help@patsnap.com