Nano emulsion of peroxide vulcanized fluororubber and polymerization method thereof
A peroxide and nanoemulsion technology, applied in the field of nanoemulsion and its polymerization, can solve the problems of reduced equipment utilization, affected production efficiency, low solid content, etc., to improve cold resistance, excellent mechanical properties and processing performance, increase The effect of flexibility
- Summary
- Abstract
- Description
- Claims
- Application Information
AI Technical Summary
Problems solved by technology
Method used
Image
Examples
Embodiment 1
[0048] Add 6kg deionized, 60g fluoroether emulsifier (C 2 f 5 [OCF 2 CF(CF 3 )] 3 OCF 2 COONH 4 ), 3g of disodium hydrogen phosphate, 10g of molecular structure with a molecular weight of 600 are (1) co-emulsifier, open the steam regulating valve, heat up the deionized water in the reactor to 80°C, feed high-purity nitrogen and vacuumize the reaction The oxygen content in the kettle is replaced to ≤30ppm. Then, under the pressure of 3.5 MPa, 45% of vinylidene fluoride, 5% of tetrafluoroethylene and 50% of perfluoromethyl vinyl ether were mixed by a compressor. Add mass fraction and be 10% potassium persulfate solution 300g, initiate polymerization reaction, polymerization pressure drops, add mixed monomer again, mass fraction is 55% vinylidene fluoride, mass fraction is 10% tetrafluoroethylene, mass fraction 35% perfluoromethyl vinyl ether is pressed into the reaction kettle through a compressor, and the pressure and temperature are maintained for reaction. After react...
Embodiment 2
[0050] In the 20L reactor, add 12kg deionization, 130g fluoroether emulsifier (C 2 f 5 [OCF 2 CF(CF 3 )] 3 OCF 2 COONH 4 ), 6g of disodium hydrogen phosphate, 20g of molecular structure with a molecular weight of 600 are (1) co-emulsifier, open the steam regulating valve, heat up the deionized water in the reactor to 80°C, feed high-purity nitrogen and vacuumize the reaction The oxygen content in the kettle is replaced to ≤30ppm. Then, under the pressure of 3.5 MPa, 45% of vinylidene fluoride, 5% of tetrafluoroethylene and 50% of perfluoromethyl vinyl ether were mixed by a compressor. Add mass fraction and be 10% potassium persulfate solution 600g, initiate polymerization reaction, polymerization pressure drops, add mixed monomer again, mass fraction is 55% vinylidene fluoride, mass fraction is 10% tetrafluoroethylene, mass fraction 35% perfluoromethyl vinyl ether is pressed into the reaction kettle through a compressor, and the pressure and temperature are maintained f...
Embodiment 3
[0052] Add 30kg deionization, 300g fluoroether emulsifier (C 2 f 5 [OCF 2 CF(CF 3 )] 3 OCF 2 COONH 4 ), 15g of disodium hydrogen phosphate, 50g of molecular structure with a molecular weight of 600 are (1) co-emulsifier, open the steam regulating valve, heat up the deionized water in the reactor to 80°C, feed high-purity nitrogen and vacuumize the reaction The oxygen content in the kettle is replaced to ≤30ppm. Then, under the pressure of 3.5 MPa, 45% of vinylidene fluoride, 5% of tetrafluoroethylene and 50% of perfluoromethyl vinyl ether were mixed by a compressor. Adding mass fraction is 1500g of 10% potassium persulfate solution, initiates polymerization reaction, and polymerization pressure drops, adds mixed monomer again, and mass fraction is 55% vinylidene fluoride, mass fraction is 10% tetrafluoroethylene, mass fraction 35% perfluoromethyl vinyl ether is pressed into the reaction kettle through a compressor, and the pressure and temperature are maintained for rea...
PUM
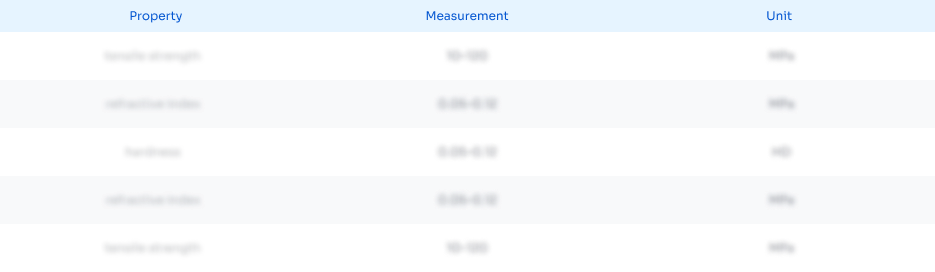
Abstract
Description
Claims
Application Information

- Generate Ideas
- Intellectual Property
- Life Sciences
- Materials
- Tech Scout
- Unparalleled Data Quality
- Higher Quality Content
- 60% Fewer Hallucinations
Browse by: Latest US Patents, China's latest patents, Technical Efficacy Thesaurus, Application Domain, Technology Topic, Popular Technical Reports.
© 2025 PatSnap. All rights reserved.Legal|Privacy policy|Modern Slavery Act Transparency Statement|Sitemap|About US| Contact US: help@patsnap.com