Preparation method of waste paint slag compatibilized wood-plastic composite material
A wood-plastic composite material and paint slag technology is applied in the field of preparation of waste paint slag compatibilizing wood-plastic composite materials, and achieves the effect of reducing production costs and realizing the unification of environmental benefits, social benefits and economic benefits.
- Summary
- Abstract
- Description
- Claims
- Application Information
AI Technical Summary
Problems solved by technology
Method used
Image
Examples
Embodiment 1
[0036] Example 1 Extrusion molding of polyethylene paint slag wood-plastic board.
[0037] Use a pulverizer or a ball mill to grind the wood fiber or paint slag into a fine powder with a fineness of 40-60 mesh, and then dry it in a vacuum drying oven (to keep the moisture content below 1.0%). Add 10Kg of the final wood fiber powder to the high mixer, then add 10 Kg of waste polyethylene plastic, 2 Kg of paint residue, 0.5Kg of lubricant (calcium stearate: 0.2Kg, zinc stearate: 0.2Kg, polyethylene Wax: 0.1Kg), 1 Kg of self-made acrylate compatibilizer, mixed at a high speed for 30 minutes and then put into a twin-screw extruder for extrusion molding.
[0038] The process temperature control of the extruder is as follows:
[0039] Main engine speed: 8.0-20.0r / min, feeding speed: 16.0-40.0r / min, pressure control: 12.5-20.0Mpa, cylinder zone 1: 190-180°C, cylinder zone 2: 180-170°C , Barrel 3 zone: 170-160°C, barrel 4 zone: 160-155°C, confluence core: 170-160V, mold temperatur...
Embodiment 2
[0040] Example 2 Extrusion molding of polyethylene / polypropylene paint slag wood-plastic board.
[0041] Use a pulverizer or a ball mill to grind the rice husk powder or paint slag into a fine powder with a fineness of 20-40 meshes, and then dry it in a vacuum drying oven (to keep the moisture content below 1.0%). Add 10Kg of dried rice husk powder to the high mixer, then add 5 Kg of waste polypropylene plastic, 10 Kg of waste polypropylene plastic, 2 Kg of paint residue, 0.5Kg of lubricant (calcium stearate: 0.2Kg, stearin Zinc acid: 0.2Kg, polyethylene wax: 0.1Kg), self-made acrylate compatibilizer 2Kg, mixed at high speed for 30 minutes to form a premix, which was put into a twin-screw extruder for extrusion molding.
[0042] The process temperature control of the extruder is as follows:
[0043] Host speed: 8.0-20.0r / min, feeding speed: 16.0-40.0r / min, pressure control: 12.5-20.0Mpa, cylinder zone 1: 200-190°C, cylinder zone 2: 190-180°C , Barrel 3 zone: 180-170°C, bar...
Embodiment 3
[0044] Example 3: Polycarbonate / polyacrylonitrile-butadiene-polystyrene (PC-ABS) paint slag wood-plastic extrusion molding.
[0045] Use a grinder or ball mill to grind corn stalk powder or paint slag into fine powders with a fineness of 20-40 meshes, and then dry them in a vacuum drying oven (to keep the moisture content below 1.0%). Add 10Kg of dried corn stalk powder to the high mixer, then add 5 Kg of waste PC-ABS plastic, 10 Kg of waste polyethylene plastic, 2 Kg of paint residue, 0.5Kg of lubricant (calcium stearate: 0.2Kg, stearin Zinc acid: 0.2Kg, polyethylene wax: 0.1Kg), self-made acrylate compatibilizer 2Kg, mixed at high speed for 30 minutes to form a premix, which was put into a twin-screw extruder for extrusion molding.
[0046] The process temperature control of the extruder is as follows:
[0047] Main engine speed: 8.0-20.0r / min, feeding speed: 16.0-40.0r / min, pressure control: 12.5-20.0Mpa, barrel zone 1: 210-200°C, barrel zone 2: 200-190°C , Barrel 3 zon...
PUM
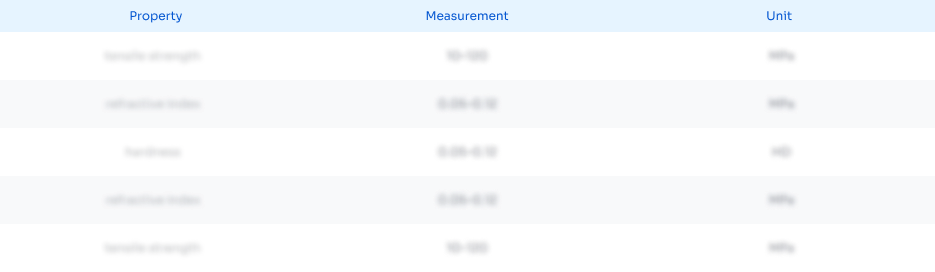
Abstract
Description
Claims
Application Information

- R&D
- Intellectual Property
- Life Sciences
- Materials
- Tech Scout
- Unparalleled Data Quality
- Higher Quality Content
- 60% Fewer Hallucinations
Browse by: Latest US Patents, China's latest patents, Technical Efficacy Thesaurus, Application Domain, Technology Topic, Popular Technical Reports.
© 2025 PatSnap. All rights reserved.Legal|Privacy policy|Modern Slavery Act Transparency Statement|Sitemap|About US| Contact US: help@patsnap.com