Low-warpage reinforced polycarbonate alloy and preparation method thereof
A polycarbonate, low warpage technology, applied in the polymer field, which can solve the problems of reducing product yield, increasing molding cycle, and loss of toughness
- Summary
- Abstract
- Description
- Claims
- Application Information
AI Technical Summary
Problems solved by technology
Method used
Image
Examples
Embodiment 1
[0034] Ratio of each component by weight: PC110065, REF-600A30, toughening agent 5. It is extruded by a twin-screw extruder with a melting temperature of 200-280°C and pelletized. The temperature of each zone is: the temperature of zone 1-2 of the twin-screw extruder is 200-280°C, the temperature of zone 3-4 is 200-280°C, the temperature of zone 5-6 is 200-280°C, and the temperature control is 7- The temperature in Zone 8 is 200-280°C, and the temperature in Zone 9-10 is 200-260°C.
Embodiment 2
[0036] Ratio of each component by weight: PC110075, REF-600A20, toughening agent 5. It is extruded by a twin-screw extruder with a melting temperature of 200-280°C and pelletized. The temperature of each zone is: the temperature of zone 1-2 of the twin-screw extruder is 200-280°C, the temperature of zone 3-4 is 200-280°C, the temperature of zone 5-6 is 200-280°C, and the temperature control is 7- The temperature in Zone 8 is 200-280°C, and the temperature in Zone 9-10 is 200-260°C.
Embodiment 3
[0038] Ratio of each component by weight: PC110085, REF-600A10, toughening agent 5. It is extruded by a twin-screw extruder with a melting temperature of 200-280°C and pelletized. The temperature of each zone is: the temperature of zone 1-2 of the twin-screw extruder is 200-280°C, the temperature of zone 3-4 is 200-280°C, the temperature of zone 5-6 is 200-280°C, and the temperature control is 7- The temperature in Zone 8 is 200-280°C, and the temperature in Zone 9-10 is 200-260°C.
PUM
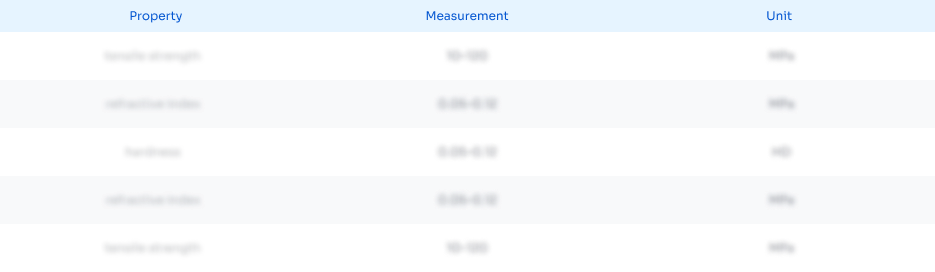
Abstract
Description
Claims
Application Information

- R&D
- Intellectual Property
- Life Sciences
- Materials
- Tech Scout
- Unparalleled Data Quality
- Higher Quality Content
- 60% Fewer Hallucinations
Browse by: Latest US Patents, China's latest patents, Technical Efficacy Thesaurus, Application Domain, Technology Topic, Popular Technical Reports.
© 2025 PatSnap. All rights reserved.Legal|Privacy policy|Modern Slavery Act Transparency Statement|Sitemap|About US| Contact US: help@patsnap.com