Low-loss microwave dielectric ceramic material and preparation method thereof
A technology of microwave dielectric ceramics and low loss, applied in the field of microwave ceramic dielectric materials and their preparation, to achieve the effect of adjustable dielectric constant and low price
- Summary
- Abstract
- Description
- Claims
- Application Information
AI Technical Summary
Problems solved by technology
Method used
Image
Examples
Embodiment 1
[0029] A method for preparing a low-loss microwave dielectric ceramic material, comprising the following steps:
[0030] Step 1: Synthesis of Mg 2 SiO 4 Crystalline powder: Basic magnesium carbonate with a purity of 99% and silicon dioxide with a purity of 99.5% are used as raw materials, and the molar ratio of Mg and Si is controlled to be Mg:Si=2.03:1. The prepared raw materials are ball-milled, and the ball-milled materials are dried at 100° C. and passed through a 40-mesh sieve. The specific ball milling process is as follows: in a nylon ball milling tank, use zirconia balls as the balls, deionized water as the ball milling solvent, and ball mill for 6 hours according to the weight ratio of materials: balls: water = 1:5:4. Pre-fire the dried material at 1260°C for 3 hours to obtain MgO containing a small amount of MgO powder 2 SiO 4 Crystal phase powder.
[0031] Step 2: Ingredients; the purity is 99% basic magnesium carbonate, 99.5% titanium dioxide, and 99.5% calciu...
Embodiment 2
[0039] A preparation method of a microwave dielectric ceramic material, comprising the following steps:
[0040] Step 1: Synthesis of Mg 2 SiO 4 Crystal phase powder; use basic magnesium carbonate with a purity of 99% and silicon dioxide with a purity of 99.5% as raw materials, and control the molar ratio of Mg and Si to Mg:Si=2.05:1 for batching. The prepared raw materials are ball-milled, and the ball-milled materials are dried at 100° C. and passed through a 40-mesh sieve. The specific ball milling process is as follows: in a nylon ball milling tank, use zirconia balls as the balls, deionized water as the ball milling solvent, and ball mill for 6 hours according to the weight ratio of materials: balls: water = 1:5:4. The dried material was pre-fired at 1220°C for 3 hours, and the Mg containing a small amount of MgO powder 2 SiO 4 Crystal phase powder.
[0041] Step 2: batching; the Mg obtained in step 1 2 SiO 4 The main crystal phase powder and basic magnesium carbon...
Embodiment 3
[0049] Step 1: Synthesis of Mg 2 SiO 4 Crystal phase powder: 99% pure magnesium carbonate and 99.5% silicon dioxide are used as raw materials, and the molar ratio of Mg and Si is controlled to be Mg:Si=2.07:1. The prepared raw materials are ball-milled, and the ball-milled materials are dried at 100° C. and passed through a 40-mesh sieve. The specific ball milling process is as follows: in a nylon ball milling tank, use zirconia balls as the balls, deionized water as the ball milling solvent, and ball mill for 6 hours according to the weight ratio of materials: balls: water = 1:5:4. The dried material was pre-fired at 1220°C for 3 hours, and the Mg containing a small amount of MgO powder 2 SiO 4 Crystal phase powder.
[0050] Step 2: batching; the Mg obtained in step 1 2 SiO 4 The main crystal phase powder and basic magnesium carbonate with a purity of 99%, 99.5% titanium dioxide, and 99.5% calcium carbonate are used as raw materials, and the proportion is controlled acc...
PUM
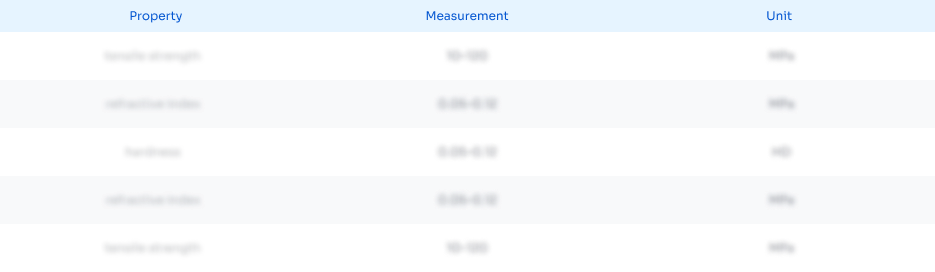
Abstract
Description
Claims
Application Information

- R&D
- Intellectual Property
- Life Sciences
- Materials
- Tech Scout
- Unparalleled Data Quality
- Higher Quality Content
- 60% Fewer Hallucinations
Browse by: Latest US Patents, China's latest patents, Technical Efficacy Thesaurus, Application Domain, Technology Topic, Popular Technical Reports.
© 2025 PatSnap. All rights reserved.Legal|Privacy policy|Modern Slavery Act Transparency Statement|Sitemap|About US| Contact US: help@patsnap.com