Preparation method of functionalized graphene oxide/epoxy resin nanocomposite
A nano-composite material and epoxy resin technology, applied in the field of polymer-based nano-composite materials, can solve the problems of less hydroxyl content, less organosilane molecules, and the influence of mechanical properties of composite materials without mentioning preparation and characterization, etc., to achieve improved Effect of mechanical and thermal properties
- Summary
- Abstract
- Description
- Claims
- Application Information
AI Technical Summary
Problems solved by technology
Method used
Image
Examples
Embodiment 1
[0042] (1) Using graphite as raw material, the prepared GO was prepared by the Hummer method, and then 500mg GO was first dispersed in toluene, ultrasonicated for 1h to obtain a graphene oxide suspension, and under the protection of nitrogen, mechanically prepared at a temperature of 70°C Under stirring, 2.4g of silane coupling agent KH560 was added dropwise to the suspension, and the reaction time was 5h. After the reaction, the black solid powder f-GO was obtained after suction filtration, washing, and drying in a vacuum oven.
[0043] (2) 0.18 g of graphene oxide (f-GO) modified by silane coupling agent in step (1) was ultrasonically treated for 30 min and dispersed in acetone, then 93.7 g of bisphenol A epoxy resin was added, planetary ball mill (250 rpm) for 6 hours to obtain the masterbatch, remove the organic solvent under vacuum (0.1MPa), and then add 86.1g of curing agent (the mass ratio of methyl hexahydrophthalic anhydride to N,N-dimethylbenzylamine is 100:1 mixture...
Embodiment 2
[0053] (1) Using graphite as raw material, the prepared GO was prepared by the Hummer method, and then 500 mg GO was first dispersed in toluene, ultrasonicated for 1 h to obtain a graphene oxide suspension, and mechanically stirred at a temperature of 70 ° C under the protection of nitrogen Next, 2.4g of silane coupling agent KH560 was added dropwise to the suspension, and the reaction time was 5h. After the reaction, the black solid powder f-GO was obtained after suction filtration, washing, and drying in a vacuum oven.
[0054] (2) 0.1625 g of silane coupling agent-modified graphene oxide (f-GO) prepared in step (1) was ultrasonically treated for 30 min. and then dispersed in acetone, then 33.79 g of bisphenol A epoxy resin was added, and the planet After ball milling (250 rpm) for 6 hours, the masterbatch was obtained. Under vacuum conditions (0.5MPa), the organic solvent was removed, and then 31.05g of curing agent were added and mixed, and cured at high temperature (120°C ...
Embodiment 3
[0060] (1) Using graphite as raw material, the prepared GO was prepared by the Hummer method, and then 500mg GO was first dispersed in toluene, ultrasonicated for 1h to obtain a graphene oxide suspension, and under the protection of nitrogen, mechanically prepared at a temperature of 70°C Under stirring, add 7.5g of methyl (γ-glycidoxy)diethoxysilane dropwise to the suspension, the reaction time is 5h, after the reaction is completed, filter with suction, wash, and dry in a vacuum oven to obtain Black solid powder f-GO.
[0061](2) 0.325 g of silane coupling agent-modified graphene oxide (f-GO) prepared in step (1) was ultrasonically treated for 30 min. and dispersed in acetone, then 33.70 g of bisphenol A epoxy resin was added, and the planet After ball milling (250 rpm) for 6 hours, the masterbatch was obtained. Under vacuum conditions (0.3MPa), the organic solvent was removed, and then 30.97g of curing agent was added and mixed, and cured at high temperature (120°C for 1h, ...
PUM
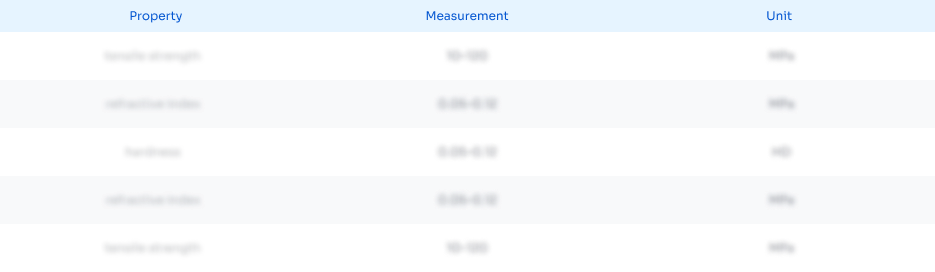
Abstract
Description
Claims
Application Information

- R&D
- Intellectual Property
- Life Sciences
- Materials
- Tech Scout
- Unparalleled Data Quality
- Higher Quality Content
- 60% Fewer Hallucinations
Browse by: Latest US Patents, China's latest patents, Technical Efficacy Thesaurus, Application Domain, Technology Topic, Popular Technical Reports.
© 2025 PatSnap. All rights reserved.Legal|Privacy policy|Modern Slavery Act Transparency Statement|Sitemap|About US| Contact US: help@patsnap.com