Low-silver-copper-based brazing filler metal and preparation method thereof
A technology of silver-copper and brazing material, which is applied in the direction of manufacturing tools, welding equipment, metal processing equipment, etc., can solve the problem of reducing the oxidation and deformation of base materials, failing to meet the needs of motors, and high silver content in high-silver copper-phosphorus brazing filler metals, etc. problems, to achieve good compactness, good fatigue performance, corrosion resistance and excellent creep strength
- Summary
- Abstract
- Description
- Claims
- Application Information
AI Technical Summary
Problems solved by technology
Method used
Examples
Embodiment 1-6
[0045] The preparation method of embodiment 1-6 comprises the following steps:
[0046] (1) Pretreatment before smelting: Before smelting, Sn is processed, and bulk Sn is prepared into filamentous Sn;
[0047] (2) Smelting: During the smelting process, Sn is added in the form of filament Sn, which increases the contact area between Sn and the melt, facilitates the uniform distribution of Sn in the melt, and solves the problem of Sn segregation; use dry plant ash As a covering agent, plant ash has the advantages of large coverage area and dense coverage, which effectively reduces the oxidation and burning loss of Sn during the smelting process, and also reduces the hydrogen absorption and oxygen content of the melt during refining;
[0048] (3) Subsequent processing of smelting: After smelting, brazing materials are obtained through continuous casting, continuous extrusion, molding, and cleaning.
Embodiment 7-12
[0049] The preparation method of embodiment 7-12 comprises the following steps:
[0050] (1) Pretreatment before smelting: Before smelting, Sn is processed, and bulk Sn is prepared into filamentous Sn;
[0051] (2) Smelting: During the smelting process, Cu, P, Ni, and Ag elements are added first when feeding, and Sn is added after complete melting. Immediately after the feeding is completed, a covering agent is added to keep warm and prevent the burning of easily oxidized elements; Sn is added in the form of filament Sn, which increases the contact area between Sn and the melt, facilitates the uniform distribution of Sn in the melt, and solves the problem of Sn segregation; using dry plant ash as a covering agent, plant ash has a large coverage area , dense coverage and other advantages, effectively reducing the oxidation and burning loss of Sn during the smelting process, and also reducing the hydrogen absorption and oxygen content of the melt during refining;
[0052] (3) S...
Embodiment 13-23
[0053] The preparation method of embodiment 13-23 comprises the following steps:
[0054] (1) Pretreatment before smelting: Before smelting, Sn is treated to prepare bulk Sn into filamentous Sn; according to the actual needs of production, Ni is first smelted with Cu to make an intermediate alloy Cu- Ni, followed by subsequent smelting;
[0055] (2) Smelting: During the smelting process, Cu-P, Cu, Cu-Ni, and Ag elements are added first when feeding, and Sn is added after complete melting. Immediately after the feeding is completed, a covering agent is added to keep warm and prevent the burning of easily oxidized elements. Sn is added in the form of filament Sn, which increases the contact area between Sn and the melt, is conducive to the uniform distribution of Sn in the melt, and solves the problem of Sn segregation; using dry plant ash as a covering agent, plant ash It has the advantages of large coverage area and compact coverage, which effectively reduces the oxidation an...
PUM
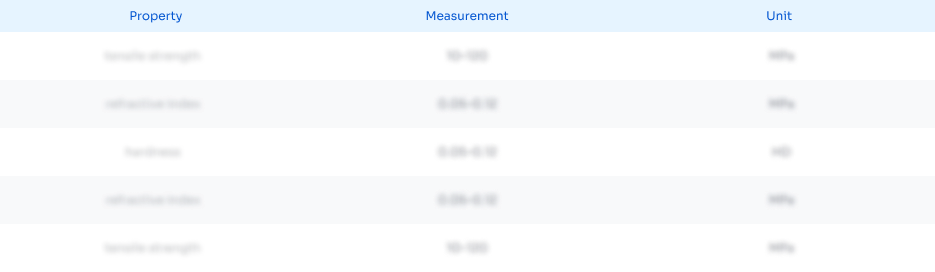
Abstract
Description
Claims
Application Information

- R&D Engineer
- R&D Manager
- IP Professional
- Industry Leading Data Capabilities
- Powerful AI technology
- Patent DNA Extraction
Browse by: Latest US Patents, China's latest patents, Technical Efficacy Thesaurus, Application Domain, Technology Topic, Popular Technical Reports.
© 2024 PatSnap. All rights reserved.Legal|Privacy policy|Modern Slavery Act Transparency Statement|Sitemap|About US| Contact US: help@patsnap.com