Method for recycling germanium from germanium-containing glass
A germanium glass and sodium germanium technology, applied in the field of germanium recovery, can solve the problems of high silicon dioxide content, difficult separation of germanium and silicon, heavy environmental pollution, etc., and achieve the effects of large specific surface area, reduced environmental pollution, and good dispersion performance.
- Summary
- Abstract
- Description
- Claims
- Application Information
AI Technical Summary
Problems solved by technology
Method used
Image
Examples
Embodiment 1
[0026] combine figure 1 As shown, 500kg of germanium-containing glass was weighed to obtain 200-mesh germanium-containing glass powder containing 0.82% germanium after coarse crushing, medium crushing, and fine grinding. Add 2500kg of NaOH aqueous solution with a mass percentage concentration of 20% to the germanium-containing glass powder, add the germanium-containing glass powder and sodium hydroxide in the NaOH aqueous solution at a ratio of 1:1, and heat it to 130°C with a steam pressure reactor. Insulated and reacted for 9 hours to obtain a mixed solution of sodium silicate and sodium germanate. Dilute the resulting mixed solution of sodium silicate and sodium germanate with water until the molar concentration of sodium silicate is 0.5M, then add 5% electrolyte sodium chloride to it by weight of the diluted solution, and then adjust the pH value to 8.0 with hydrochloric acid , after aging for 2 hours, solid-liquid separation, solid drying to obtain high-purity amorphous ...
Embodiment 2
[0028] 200-mesh germanium-containing glass powder containing about 0.93% germanium is obtained by weighing 300kg of germanium-containing glass through coarse crushing, medium crushing, and fine grinding. Add 1500kg of NaOH aqueous solution with a mass percentage concentration of 10% to the germanium-containing glass powder, the mass ratio of the germanium-containing glass powder to sodium hydroxide in the NaOH aqueous solution is 2:1, heat it to 200°C with an electric heating pressure reactor, and keep it warm for 5 Hours, a mixed solution of sodium silicate and sodium germanate was obtained. Dilute the resulting mixed solution of sodium silicate and sodium germanate with water until the molar concentration of sodium silicate is 0.2 M, then add 10% electrolyte sodium bromide of the weight of the diluted solution to it, and then neutralize it to the pH value with hydrochloric acid After aging for 2 hours, the solid and liquid were separated, and the solid was dried to obtain hi...
Embodiment 3
[0030] 200-mesh germanium-containing glass powder containing 1.63% germanium is obtained by taking 500kg of germanium-containing glass through coarse crushing, medium crushing and fine grinding. Add 2200kg of NaOH aqueous solution with a mass percentage concentration of 15% to the germanium-containing glass powder, and the mass ratio of the germanium-containing glass powder to sodium hydroxide in the NaOH aqueous solution is 1.5:1. Heat it to 150°C with an electric heating pressure reactor, and heat preservation reaction for 8 hours, a mixed solution of sodium silicate and sodium germanate was obtained. Dilute the mixed solution of sodium silicate and sodium germanate with water until the molar concentration of sodium silicate is 1M, then add electrolyte potassium bromide of 20% of the solution weight after dilution, and then adjust the pH value to 9.0 with hydrochloric acid. After aging for 2 hours, the solid and liquid were separated, and the solid was dried to obtain high-p...
PUM
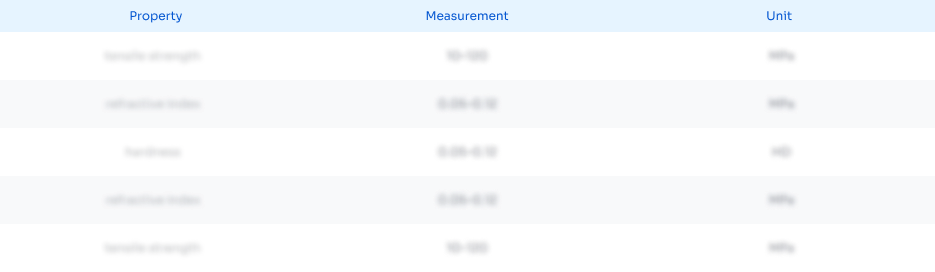
Abstract
Description
Claims
Application Information

- R&D
- Intellectual Property
- Life Sciences
- Materials
- Tech Scout
- Unparalleled Data Quality
- Higher Quality Content
- 60% Fewer Hallucinations
Browse by: Latest US Patents, China's latest patents, Technical Efficacy Thesaurus, Application Domain, Technology Topic, Popular Technical Reports.
© 2025 PatSnap. All rights reserved.Legal|Privacy policy|Modern Slavery Act Transparency Statement|Sitemap|About US| Contact US: help@patsnap.com