A finishing grinding method for large precision threaded holes
A technology of precision thread and grinding method, applied in the direction of grinding machine tools, grinding tools, grinding devices, etc., can solve the problems of large threaded holes, large risks, high processing risks, difficult to guarantee the uniformity of polishing, etc., and achieve excellent thread surface. Quality, simple and quick operation process, extra removal effect with little margin
- Summary
- Abstract
- Description
- Claims
- Application Information
AI Technical Summary
Problems solved by technology
Method used
Image
Examples
Embodiment Construction
[0024] The method for finishing and grinding large precision threaded holes of the present invention is mainly aimed at large threaded holes such as M155 threaded holes, especially when the surface quality of the threads in the threaded holes is required to be very high.
[0025] A method for finishing and grinding large precision threaded holes of the present invention comprises the following steps:
[0026] (1) Check and clean the threaded holes, determine the amount of grinding and select the appropriate size of grinding paste;
[0027] (2) Apply grinding paste to the threaded surface and / or threaded hole of the grinding rod;
[0028] (3) Slowly screw the grinding rod body into the threaded hole, and repeatedly rotate the grinding rod body back and forth for grinding;
[0029] (4) According to the amount of grinding in step (1), after the grinding time or the number of rotations of the grinding rod reaches a predetermined value, stop grinding and exit the grinding rod;
...
PUM
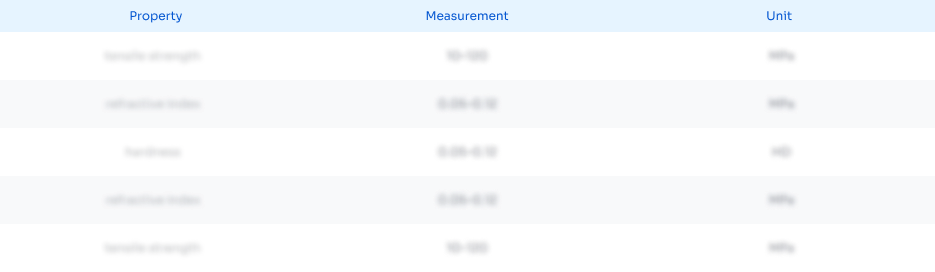
Abstract
Description
Claims
Application Information

- R&D
- Intellectual Property
- Life Sciences
- Materials
- Tech Scout
- Unparalleled Data Quality
- Higher Quality Content
- 60% Fewer Hallucinations
Browse by: Latest US Patents, China's latest patents, Technical Efficacy Thesaurus, Application Domain, Technology Topic, Popular Technical Reports.
© 2025 PatSnap. All rights reserved.Legal|Privacy policy|Modern Slavery Act Transparency Statement|Sitemap|About US| Contact US: help@patsnap.com