Heat bonding non-woven fabric and preparation method thereof
A non-woven, thermal bonding technology, used in non-woven fabrics, textiles and papermaking, fabric surface trimming and other directions, can solve the problems of reducing fiber cohesion, poor comfort, easy deformation, etc., to improve hygroscopicity and comfort, excellent antibacterial function, the effect of preventing side leakage and slippage
- Summary
- Abstract
- Description
- Claims
- Application Information
AI Technical Summary
Problems solved by technology
Method used
Examples
Embodiment 1
[0035] Using 20wt% cotton fiber and 80wt% ES fiber as raw materials, the above-mentioned fiber raw materials are sequentially opened and mixed, carded, hot-air bonded, cooled and shaped, hot-rolled and solidified, and coiled to obtain the product, wherein:
[0036] In the hot air bonding process, the degree of melting of thermoplastic fibers is 50%;
[0037] The equipment adopted in the cooling and shaping process is two relative cooling rollers, and the cooling temperature of the cooling rollers is 50°C;
[0038] The hot pressing roll in the hot rolling solidification process includes an upper hot pressing roll and a lower hot pressing roll. The hot rolling method is a combination of line and surface contact hot rolling. Contact hot rolling, the lower hot pressing roller is provided with net-like protrusions for printing on the surface of the non-woven fabric, and the height of the net-like protrusions is 3 mm;
[0039] In the carding process, the fiber laying method adopts ...
Embodiment 2
[0043] The preparation method of thermally bonded non-woven fabric adopts 40wt% viscose fiber and 60wt% polyester fiber as raw materials, and the fiber raw materials are sequentially opened and mixed, carded, hot-air bonded, cooled and shaped, hot-rolled and solidified, and rolled into rolls. Products are obtained, wherein:
[0044] In the hot air bonding process, the degree of melting of thermoplastic fibers is 60%;
[0045] The equipment adopted in the cooling and shaping process is two relative cooling rollers, and the cooling temperature of the cooling rollers is 40°C;
[0046] The hot pressing roll in the hot rolling solidification process includes an upper hot pressing roll and a lower hot pressing roll. The hot rolling method is a combination of line and surface contact hot rolling. Contact hot rolling, the lower hot pressing roller is provided with net-like protrusions for printing on the surface of the non-woven fabric, and the height of the net-like protrusions is 4...
Embodiment 3
[0051] The preparation method of thermally bonded non-woven fabric adopts 5wt% wool fiber and 95wt% polypropylene fiber as raw materials, and the fibers are sequentially opened, carded, hot-air bonded, cooled and shaped, hot-rolled and solidified, and rolled into a roll. products, including:
[0052] In the hot air bonding process, the degree of melting of thermoplastic fibers is 40% to 60%;
[0053] The equipment used in the cooling and shaping process is two opposite cooling rollers, and the cooling temperature of the cooling rollers is 40°C to 60°C;
[0054] The hot pressing roll in the hot rolling solidification process includes an upper hot pressing roll and a lower hot pressing roll. The hot rolling method is a combination of line and surface contact hot rolling. Contact hot rolling, the lower hot pressing roller is provided with net-like protrusions for printing on the surface of the non-woven fabric, and the height of the net-like protrusions is 2 mm;
[0055] In the...
PUM
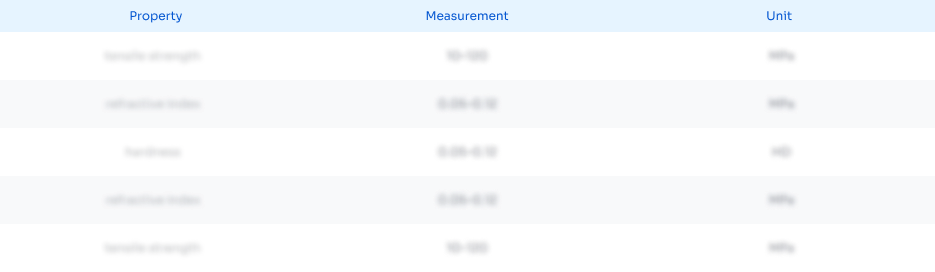
Abstract
Description
Claims
Application Information

- R&D Engineer
- R&D Manager
- IP Professional
- Industry Leading Data Capabilities
- Powerful AI technology
- Patent DNA Extraction
Browse by: Latest US Patents, China's latest patents, Technical Efficacy Thesaurus, Application Domain, Technology Topic, Popular Technical Reports.
© 2024 PatSnap. All rights reserved.Legal|Privacy policy|Modern Slavery Act Transparency Statement|Sitemap|About US| Contact US: help@patsnap.com