Environment-friendly high-performance cement and production method thereof
A high-performance, cement technology, used in cement production and other directions, can solve the problems of inability to meet the construction industry, low concrete fluidity, poor filling effect, etc., and achieve the effect of shortening grinding time, improving ball milling efficiency, and small equipment footprint.
- Summary
- Abstract
- Description
- Claims
- Application Information
AI Technical Summary
Problems solved by technology
Method used
Image
Examples
Embodiment 1
[0035] 50 parts of the mixed material composed of thermal power plant waste slag and limestone are added to the high-efficiency and energy-saving dryer from the homogenization field, and the heat generated by coal combustion is used to rotate and dry to a moisture content of 3-5%, and it is ground to a particle size of 200 mesh by a ball mill. Put it into the homogenization warehouse, add 38 parts of cement clinker, 6 parts of powdered gypsum, 0.04 part of triethanolamine, 5 parts of sodium hydroxide and aluminum hydroxide, put it into the grinder after homogenization, and put it into the ball mill during the grinding process 0.5MPa high-pressure water is sprayed inside to make the temperature of the grinding process 130±2°C. The material coming out of the grinder is put into the storage bin, put into the homogenization bin, and 0.05 parts of powdered ethylene-vinyl acetate copolymer is added. Material, 0.1 part of polyether defoamer, 0.04 part of sodium carboxymethylcellulose ...
Embodiment 2
[0037] 54 parts of manganese and manganese alloy factory waste slag and limestone mixed materials are added to the high-efficiency energy-saving dryer from the homogenization field, and the heat generated by coal combustion is used to rotate and dry to a moisture content of 3-5%, and to be ground to a particle size of 250 mesh by a ball mill. , put it into the homogenization storehouse, add 36 parts of cement clinker, 8 parts of powdered gypsum, 0.03 parts of triethanolamine phosphate, and 3 parts of alum. Enter 1MPa high-pressure water to make the temperature of the grinding process 100±2°C. Put the material out of the grinder into the storage bin, put it into the homogenization warehouse, add 0.05 parts of powdered ethylene-vinyl acetate copolymer, 0.05 One part of polytetramethylsiloxane defoamer, 0.04 part of sodium polyacrylate and 0.3 part of water-soluble sodium polystyrene sulfonate were homogenized to obtain green cement.
Embodiment 3
[0039]57 parts of mixed material composed of iron and steel smelter waste slag and limestone are added to the high-efficiency energy-saving dryer from the homogenization field, and the heat generated by coal combustion is used to rotate and dry to a moisture content of 3-5%. Put it into the homogenization warehouse, add 32 parts of cement clinker, 7 parts of powdered gypsum, 0.05 part of diethanolamine phosphate, 3 parts of alum and 1 part of borax, put it into the grinder after homogenization treatment, and put it into the ball mill during the grinding process 0.8MPa high-pressure water is sprayed inside to make the temperature of the grinding process 110±2°C. The material coming out of the grinder is put into the storage bin and put into the homogenization warehouse. Add 0.1 part of powdered polyvinyl acetate, 0.06 1 part of polytetramethylsiloxane defoamer, 0.05 part of guar gum, gelatinized starch and 0.4 part of sodium lignosulfonate were homogenized to obtain green cement...
PUM
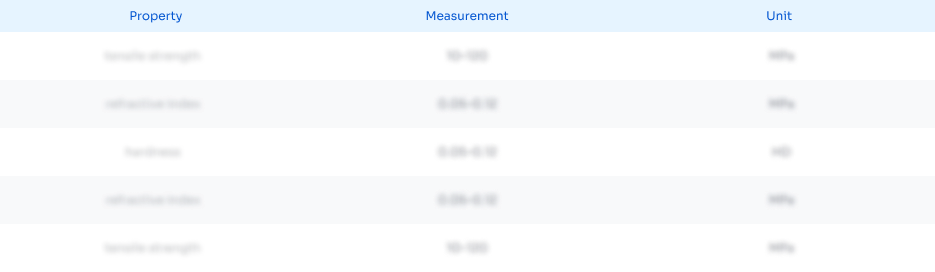
Abstract
Description
Claims
Application Information

- R&D
- Intellectual Property
- Life Sciences
- Materials
- Tech Scout
- Unparalleled Data Quality
- Higher Quality Content
- 60% Fewer Hallucinations
Browse by: Latest US Patents, China's latest patents, Technical Efficacy Thesaurus, Application Domain, Technology Topic, Popular Technical Reports.
© 2025 PatSnap. All rights reserved.Legal|Privacy policy|Modern Slavery Act Transparency Statement|Sitemap|About US| Contact US: help@patsnap.com