Casting technology of stainless steel casting
A casting process, stainless steel technology, applied in the direction of manufacturing tools, casting molding equipment, casting molds, etc., can solve the problems of failing to meet the dimensional accuracy requirements of small-sized castings, unable to ensure complete mold filling, rough casting surfaces, etc., and achieve production costs. Low, easy to operate, good quality effect
- Summary
- Abstract
- Description
- Claims
- Application Information
AI Technical Summary
Problems solved by technology
Method used
Examples
Embodiment 1
[0027] A casting process for stainless steel castings, comprising the following steps in turn:
[0028] The first step: make a mold according to the appearance of the stainless steel casting, combine the mold with the pouring system mold to form a module, fix the module in the steel sleeve, and the edge of the module is 5-10mm away from the inner wall of the steel sleeve;
[0029] Step 2: Prepare the slurry, dilute the modified phosphate with water and mix it evenly, add the composite powder into the phosphate solution, stir with a mixer at low speed and then at high speed to form a slurry, the stirring time is 10-15min, and mix the slurry Put it in the vacuum hood under the state of micro-shock and pump the vacuum for 2-4 minutes;
[0030] The third step: grouting modeling, inject the prepared slurry into the steel sleeve with wax model, and place it in the vacuum cover, vacuumize for 4 minutes under the state of micro-shock, and then let the steel sleeve stand for 6-7 hours ...
PUM
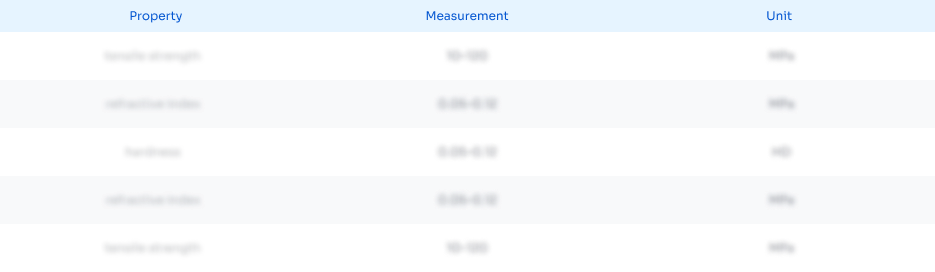
Abstract
Description
Claims
Application Information

- R&D
- Intellectual Property
- Life Sciences
- Materials
- Tech Scout
- Unparalleled Data Quality
- Higher Quality Content
- 60% Fewer Hallucinations
Browse by: Latest US Patents, China's latest patents, Technical Efficacy Thesaurus, Application Domain, Technology Topic, Popular Technical Reports.
© 2025 PatSnap. All rights reserved.Legal|Privacy policy|Modern Slavery Act Transparency Statement|Sitemap|About US| Contact US: help@patsnap.com