Compact electro-fused corundum-spinel ladle casting material
A technology of ladle casting and fused corundum, applied in the field of unshaped refractory materials, can solve the problems of damage to the ladle body, cracking of ladle castables, unsatisfactory thermal shock stability, etc., and achieves reduction of apparent pores, improvement of strength, and prevention of penetration. and erosion effects
- Summary
- Abstract
- Description
- Claims
- Application Information
AI Technical Summary
Problems solved by technology
Method used
Image
Examples
Embodiment Construction
[0009] A ladle lining (melt pool pouring) applied to pouring of 100t ladle castables.
[0010] In terms of weight percentage, dense fused corundum particle size is 15-20% for 25-15mm, 20-25% for 15-8mm, 20-30% for 8-1mm, 5-15% for ≤0.074mm. Spinel particle size 1-0.5mm is 5-15%, sintered spinel particle size ≤0A074mm is 1-15%, alumina fine powder is 1-10%, magnesia fine powder ≤0.088mm is 0.5-5%, silicon Micro powder is 0.05-0.5%, sodium tripolyphosphate is 0.1-0.5%, polypropylene fiber is 0.01-0.1%, calcium aluminum magnesium oxide cement binder is 5-15%, and the sum of the above components is 100%. After fully stirring evenly, add <4% tap water, stir evenly, pour into molding, cure, bake, and remove the mold to obtain the inner lining of the ladle.
[0011] Example Dense fused corundum - main technical performance table of spinel ladle castable
[0012]
PUM
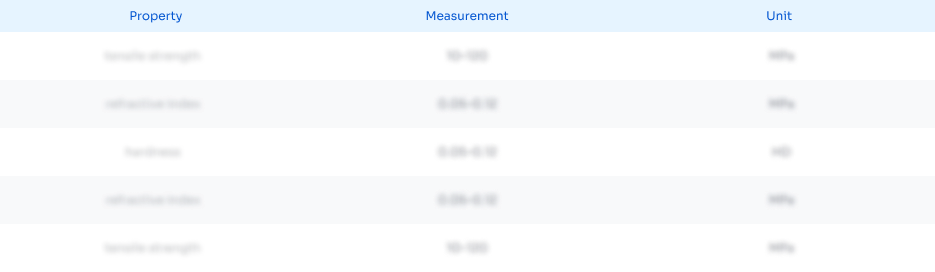
Abstract
Description
Claims
Application Information

- Generate Ideas
- Intellectual Property
- Life Sciences
- Materials
- Tech Scout
- Unparalleled Data Quality
- Higher Quality Content
- 60% Fewer Hallucinations
Browse by: Latest US Patents, China's latest patents, Technical Efficacy Thesaurus, Application Domain, Technology Topic, Popular Technical Reports.
© 2025 PatSnap. All rights reserved.Legal|Privacy policy|Modern Slavery Act Transparency Statement|Sitemap|About US| Contact US: help@patsnap.com