Method for smelting high-grade pipe line steel with RH single-link process
A high-grade, pipeline steel technology, applied in the field of steelmaking, can solve the problems of lower temperature, high cost, and long cycle in the refining process, and achieve the effects of simplifying the smelting process, making up for heat loss, and reducing production costs
- Summary
- Abstract
- Description
- Claims
- Application Information
AI Technical Summary
Problems solved by technology
Method used
Image
Examples
Embodiment 1
[0031] During the tapping process of the converter, before the tapping amount reaches 1 / 3 stage, aluminum and iron are added to the molten steel, and the mass percentage of aluminum in the molten steel after deoxidation is controlled to be 0.13% (see Table 1); the tapping amount reaches 1 / 3 to 2 / 3 stage, add lime 8kg / t steel to molten steel. After the steel tapping is completed, the top gun is used to blow argon gas to the molten steel for strong stirring, the intensity of argon blowing is controlled at 5NL / min / t steel, and the time of argon blowing is 8 minutes. After blowing argon on the molten steel, carry out RH vacuum treatment. After evacuating for 3.5 minutes and the vacuum degree is 984Pa, add desulfurizer to the molten steel through the vacuum silo. After adding the desulfurizer, keep the vacuum degree at 992Pa. RH vacuum cycle treatment of molten steel for 3 minutes (see Table 2), further deep desulfurization of molten steel. Among them, the addition amount of desu...
Embodiment 2
[0033] During the tapping process of the converter, before the tapping amount reaches 1 / 3 stage, aluminum and iron are added to the molten steel, and the mass percentage of aluminum in the molten steel after deoxidation is controlled to be 0.12% (see Table 1); the tapping amount reaches 1 From / 3 to 2 / 3 stage, add lime 9kg / t steel to molten steel. After tapping, use the top lance to blow argon gas to the molten steel for strong stirring, the intensity of argon blowing is controlled to 7NL / min / t steel, and the argon blowing time is 5 minutes. After blowing argon to the molten steel, carry out RH vacuum treatment. After evacuating for 4.5 minutes and the vacuum degree is 923Pa, add desulfurizer to the molten steel through the vacuum silo. After adding the desulfurizer, keep the vacuum degree at 984Pa, continue RH vacuum cycle treatment of molten steel for 3 minutes (see Table 2), further deep desulfurization of molten steel. Among them, the addition amount of desulfurizer is 4....
Embodiment 3
[0035] During the tapping process of the converter, before the tapping amount reaches 1 / 3 stage, aluminum and iron are added to the molten steel, and the mass percentage of aluminum in the molten steel after deoxidation is controlled to be 0.15% (see Table 1); the tapping amount reaches 1 / 3 to 2 / 3 stage, add lime 10kg / t steel to molten steel. After the steel tapping is completed, the top gun is used to blow argon gas to the molten steel for strong stirring, the intensity of argon blowing is controlled at 6NL / min / t steel, and the time of argon blowing is 7 minutes. After blowing the molten steel with argon, carry out RH vacuum treatment. After evacuating for 4.5 minutes and the vacuum degree is 977Pa, add desulfurizer to the molten steel through the vacuum silo. After adding the desulfurizer, keep the vacuum degree at 992Pa, continue RH vacuum cycle treatment of molten steel for 3 minutes (see Table 2), further deep desulfurization of molten steel. Among them, the addition am...
PUM
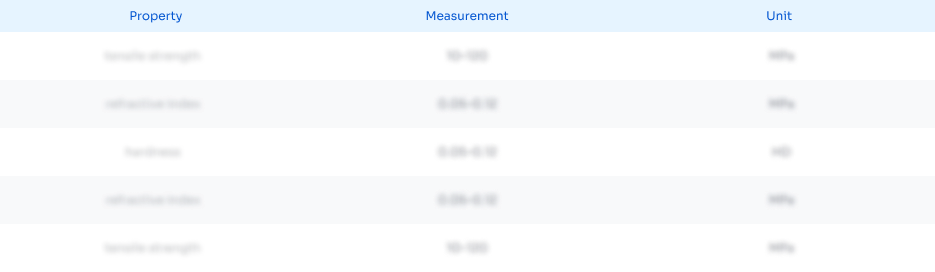
Abstract
Description
Claims
Application Information

- Generate Ideas
- Intellectual Property
- Life Sciences
- Materials
- Tech Scout
- Unparalleled Data Quality
- Higher Quality Content
- 60% Fewer Hallucinations
Browse by: Latest US Patents, China's latest patents, Technical Efficacy Thesaurus, Application Domain, Technology Topic, Popular Technical Reports.
© 2025 PatSnap. All rights reserved.Legal|Privacy policy|Modern Slavery Act Transparency Statement|Sitemap|About US| Contact US: help@patsnap.com