Powder metallurgy gear disk and manufacturing method thereof
A powder metallurgy and gear plate technology, applied in the field of powder metallurgy, can solve the problems that other properties of the product fail to meet the requirements for use, cracking in the final axis area, etc., and achieve the effects of good microstructure, high production efficiency, and good practicability.
- Summary
- Abstract
- Description
- Claims
- Application Information
AI Technical Summary
Problems solved by technology
Method used
Examples
Embodiment Construction
[0015] specific implementation plan
[0016] The present invention will be described in detail below through specific examples.
[0017] A powder metallurgy gear disc, made of the following raw materials in parts by weight (kg): Ni1.2, Mo2.3, Cu0.3, Bi0.5, Tb0.1, Al2.1, Sn1.4, stearic acid Zinc 3.2, iron powder 92, additive 1;
[0018] The auxiliary agent is made of the following raw materials in parts by weight (kg): iron powder 4, zinc oxide 2, titanium dioxide 2, sodium metaphosphate 2, kaolin powder 6, aluminum nitride powder 1, silane coupling agent KH550 3, boron Chromium 6, maleic anhydride 2, dimethyl silicone oil 2, aluminate coupling agent DL-411 3, zinc cyanurate 2; the preparation method is to mix iron powder, zinc oxide, titanium dioxide, sodium metaphosphate, kaolin Powder and aluminum nitride powder are mixed, ground into 200-300 mesh powder, then mixed with silane coupling agent KH550, pressed at 10-15Mpa to form a billet, and then sent to 920-950°C for 3-4 h...
PUM
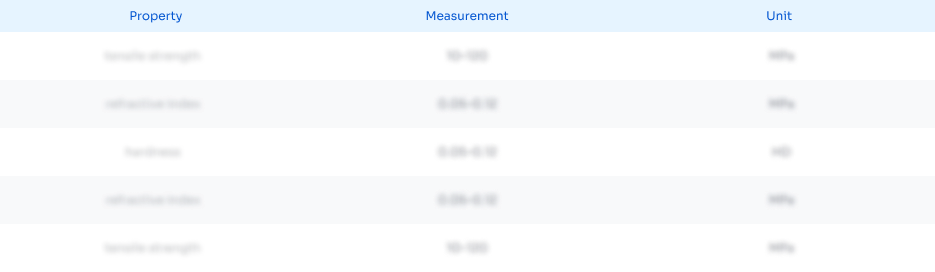
Abstract
Description
Claims
Application Information

- R&D
- Intellectual Property
- Life Sciences
- Materials
- Tech Scout
- Unparalleled Data Quality
- Higher Quality Content
- 60% Fewer Hallucinations
Browse by: Latest US Patents, China's latest patents, Technical Efficacy Thesaurus, Application Domain, Technology Topic, Popular Technical Reports.
© 2025 PatSnap. All rights reserved.Legal|Privacy policy|Modern Slavery Act Transparency Statement|Sitemap|About US| Contact US: help@patsnap.com