Continuous process for producing manganese-silicon alloy and slag rich in silicomanganese and producing micro-and low-carbon manganese-silicon alloy by utilization of slag rich in silicomanganese
A technology of silicon-rich manganese slag and manganese-silicon alloy, which is applied in the continuous process field of producing micro- and low-carbon manganese-silicon alloys, can solve the problems of high price, high alkalinity, and increased cost, and achieve the improvement of comprehensive recovery rate and the reduction of production cost, effective use of resources
- Summary
- Abstract
- Description
- Claims
- Application Information
AI Technical Summary
Problems solved by technology
Method used
Examples
Embodiment 1
[0020] Embodiment 1: A kind of production manganese-silicon alloy and silicon-rich manganese slag of embodiment 1 and utilize silicon-rich manganese slag to produce the continuous process of micro, low-carbon manganese-silicon alloy, adopt 16000KVA submerged heat electric furnace production grade to be: the manganese silicon of FeMn68Si18 The alloy and silicon-manganese-rich slag contain more than 20 wt% manganese. Raw materials used: 300 kg of coke with a fixed carbon content of 84.21wt%, SiO 2 Mix 300 kg of silica with a content of 98.18 wt%, 200 kg of manganese ore with a manganese content of 40.17 wt%, 500 kg of manganese ore with a manganese content of 37.95 wt%, and 300 kg of manganese ore with a manganese content of 46.93 wt%. 18 batches of raw materials are continuously added to the furnace, and the alloy and slag are released from the furnace after 2 hours of continuous smelting. During this period, the basicity of the slag was 0.28, and the recovery rate of silica ...
Embodiment 2
[0023] Embodiment 2: a kind of production manganese-silicon alloy and silicon-rich manganese slag of embodiment 2 and utilize silicon-rich manganese slag to produce the continuous process of micro, low-carbon manganese-silicon alloy, adopt 12500KVA closed-type submerged heat electric furnace production grade to be: FeMn68Si18 Manganese-silicon alloy and silicon-rich manganese slag contain more than 20 wt% manganese. Raw materials used: 200 kg of coke with a fixed carbon content of 86.12wt%, SiO 2200 kg of silica with 98.86 wt% content, 280 kg of manganese ore with 49.01 wt% manganese content, 245 kg of manganese ore with 41.9 wt% manganese content, 105 kg of manganese ore with 37.67 wt% manganese content, 44.6 wt% manganese ore 70 kg is mixed into a batch of materials, and about 15 batches of raw materials are continuously added into the furnace through the silo, and the alloy and slag are released from the furnace after about three hours of continuous smelting. During this ...
Embodiment 3
[0026] Embodiment 3: A kind of production manganese-silicon alloy and silicon-rich manganese slag of embodiment 3 and utilize silicon-rich manganese slag to produce the continuous process of micro, low-carbon manganese-silicon alloy, at first adopt 25000KVA submerged heat electric furnace production grade to be: the manganese of FeMn68Si18 The silicon alloy and silicon-manganese-rich slag contain more than 20 wt% manganese. Raw materials used: 248 kg of coke with a fixed carbon content of 84.32 wt%, SiO 2 240 kg of silica with 98.65 wt% content, 50 kg of manganese ore with 43.4 wt% manganese content, 300 kg of manganese ore with 37.27 wt% manganese content, 50 kg of manganese ore with 47.7 wt% manganese content, 400 kg of manganese ore with 49.2 wt% manganese content Mixed into a batch of materials, 26 batches of raw materials are continuously added into the furnace through the silo, and the alloy and slag are released from the furnace after six hours of continuous smelting. ...
PUM
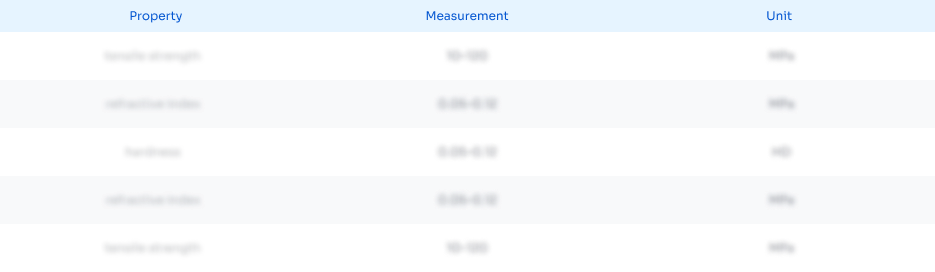
Abstract
Description
Claims
Application Information

- R&D Engineer
- R&D Manager
- IP Professional
- Industry Leading Data Capabilities
- Powerful AI technology
- Patent DNA Extraction
Browse by: Latest US Patents, China's latest patents, Technical Efficacy Thesaurus, Application Domain, Technology Topic, Popular Technical Reports.
© 2024 PatSnap. All rights reserved.Legal|Privacy policy|Modern Slavery Act Transparency Statement|Sitemap|About US| Contact US: help@patsnap.com