Method for separating iron, vanadium and titanium from schreyerite
A separation method, technology of vanadium-titanium ore, applied in the separation of vanadium and titanium, iron in vanadium-titanium ore, can solve the problems of long process and high energy consumption, achieve high-efficiency separation, reduce energy consumption, and avoid high-temperature reduction and melting Effect
- Summary
- Abstract
- Description
- Claims
- Application Information
AI Technical Summary
Problems solved by technology
Method used
Image
Examples
example 1
[0031] Vanadium-titanium ore (containing TFe54.2%, V 2 o 5 0.62%, TiO 2 13.7%, particle size2 48.6%), the obtained magnetic material is separated by a second magnetic separation through a drum magnetic separator with a magnetic field strength of 0.03T to obtain a magnetic material (that is, the first iron-rich material, which contains TFe91.5%), and the obtained The non-magnetic material is re-selected by a shaker after being pulped by ball milling, and the second titanium-rich material (containing TiO 2 42.1%) and the second iron-rich material (which contains TFe55.7%).
example 2
[0033] Vanadium-titanium ore (containing TFe30.5%, TiO 2 47.2%, particle size 2 75.2%), and the obtained magnetic material is separated by a second magnetic separation through a drum magnetic separator with a magnetic field strength of 0.02T to obtain a magnetic material (that is, the first iron-rich material, which contains TFe87.5%), and the obtained The non-magnetic material is re-selected by a shaker after being pulped by ball milling, and the second titanium-rich material (containing TiO 2 57.5%) and the second iron-rich material (which contains TFe51.8%).
Embodiment 3
[0035] Vanadium-titanium ore (containing TFe53.1%, V 2 o 5 0.57%, TiO 2 12.8%, particle size2 52.0%), the obtained magnetic material is separated by a second magnetic separation through a drum magnetic separator with a magnetic field strength of 0.025T to obtain a magnetic material (that is, the first iron-rich material, which contains TFe90.2%), and the obtained The non-magnetic material is re-selected by a shaker after being pulped by ball milling, and the second titanium-rich material (containing TiO 2 43.7%) and the second iron-rich material (which contains TFe57.2%).
[0036] In summary, the vanadium-titanium magnetite, industrial sodium sulfate, coal powder and other raw materials used in the method for separating iron, vanadium and titanium in the vanadium-titanium ore of the present invention are cheap and easy to get, and the method can effectively convert vanadium-titanium The iron, vanadium and titanium resources in the mine are extracted, the process flow is sim...
PUM
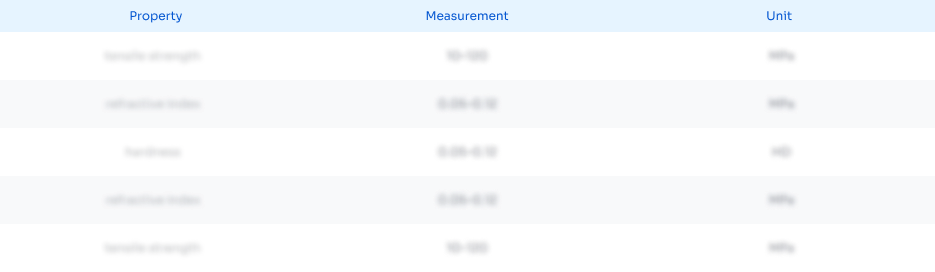
Abstract
Description
Claims
Application Information

- R&D
- Intellectual Property
- Life Sciences
- Materials
- Tech Scout
- Unparalleled Data Quality
- Higher Quality Content
- 60% Fewer Hallucinations
Browse by: Latest US Patents, China's latest patents, Technical Efficacy Thesaurus, Application Domain, Technology Topic, Popular Technical Reports.
© 2025 PatSnap. All rights reserved.Legal|Privacy policy|Modern Slavery Act Transparency Statement|Sitemap|About US| Contact US: help@patsnap.com