Method for producing gas-based directly reduced iron by utilizing non-catalytic conversion of coke-oven gas, and system thereof
A coke oven gas, non-catalytic technology, applied in the direction of furnaces, shaft furnaces, furnace types, etc., can solve the problems of high energy consumption, low unsafe utilization of methane, high sulfur content of reduced iron, etc., and achieve high effective gas content, Good energy saving and high iron reduction rate and reduction speed effect
- Summary
- Abstract
- Description
- Claims
- Application Information
AI Technical Summary
Problems solved by technology
Method used
Image
Examples
Embodiment 1
[0054] This example provides a system for producing gas-based direct reduced iron by non-catalytic conversion of coke oven gas, the structure of which is as follows figure 1 shown. The system includes a purifier 1, a first fine desulfurization tower 2, a reformer 3, a gas mixer 4, a shaft furnace 5, a scrubber 6, a second fine desulfurization tower 7, a decarburization tower 8, and a heater 9, wherein:
[0055] The purifier 1 is provided with a coke oven gas input port, and its outlet is connected with the first fine desulfurization tower 2;
[0056] The first fine desulfurization tower 2 is equipped with CO 2 / H 2 O inlet, its outlet is connected with reforming furnace 3, and other gas input pipelines are provided on the connecting pipeline of the two;
[0057] The gas mixer 4 is respectively provided with an oxygen-containing gas inlet and a CO 2 / H 2 O inlet, its outlet is connected with reforming furnace 3;
[0058] The outlet of reforming furnace 3 is connected with...
Embodiment 2
[0068] This embodiment provides a method for producing gas-based direct reduced iron by non-catalytic conversion of coke oven gas, which includes the following steps, and its process is as follows figure 2 As shown, you can use figure 1 The system shown:
[0069] The flow rate of raw coke oven gas is 22500Nm 3 / h, wherein, by volume ratio, the methane content is about 20%, the hydrogen content is about 60%, and the rest is a small amount of CO 2 , CO, N 2 and C 2 + components, the total sulfur content is less than 300ppm;
[0070]The raw coke oven gas enters the purifier 1 and undergoes dedusting, deoiling and compression, then heats up to 200°C, and enters the first fine desulfurization tower 2 under a pressure of 1.2MPa, which is the fine desulfurization reactor for hydrogen adsorption desulfurization. There are two reactors in total, one can be opened and the other can be regenerated, and it can also be used in series and parallel. The fine desulfurizer contains 15wt...
Embodiment 3
[0077] This embodiment provides a method for producing gas-based direct reduced iron by non-catalytic conversion of coke oven gas, which includes the following steps, and its process is as follows image 3 Shown:
[0078] The flow rate of raw coke oven gas is 26000Nm 3 / h, wherein, in terms of volume ratio, the content of methane is about 25%, the content of hydrogen is about 56%, and a small amount of CO 2 , CO, N 2 and C 2 + components, the total sulfur content is less than 350ppm;
[0079] After dust removal, deoiling and compression, the raw coke oven gas is heated up to 300°C by heat exchange, and enters the hydrogen adsorption fine desulfurization reactor under a pressure of 1.0 MPa. Two reactors are used, one can be opened and the other can be regenerated, or Used in series and parallel, each equipped with hydrogen adsorption fine desulfurizer 56m 3 (The hydrogen adsorption fine desulfurizer is CUPB-XTS series hydrogen adsorption desulfurizer, produced by Dongying...
PUM
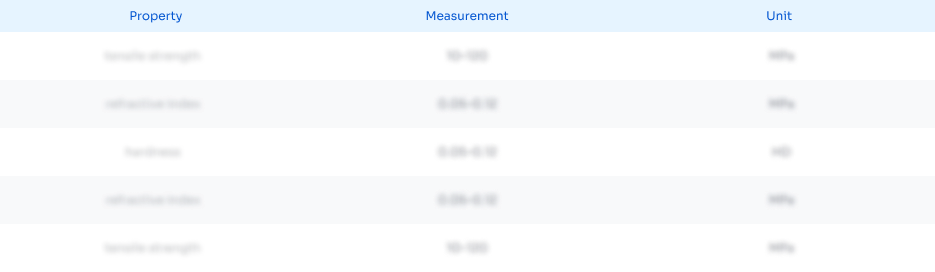
Abstract
Description
Claims
Application Information

- Generate Ideas
- Intellectual Property
- Life Sciences
- Materials
- Tech Scout
- Unparalleled Data Quality
- Higher Quality Content
- 60% Fewer Hallucinations
Browse by: Latest US Patents, China's latest patents, Technical Efficacy Thesaurus, Application Domain, Technology Topic, Popular Technical Reports.
© 2025 PatSnap. All rights reserved.Legal|Privacy policy|Modern Slavery Act Transparency Statement|Sitemap|About US| Contact US: help@patsnap.com