Lignite wax oxidizing and refining method
A technology of oxidative refining and montan wax, which is applied in the recovery/refining of mineral wax, petroleum industry, etc. It can solve the problems of destroying the chromophoric group or structure of montan wax, adding ammonia water to stimulate the smell, and the product cannot be completely decolorized. Excellent wax quality, short reaction time and high yield
- Summary
- Abstract
- Description
- Claims
- Application Information
AI Technical Summary
Problems solved by technology
Method used
Image
Examples
Embodiment 1
[0017] 1. First add 1kg of defatted montan wax to the reaction kettle, then mix and dissolve 200g of peracetic acid solution with a mass percentage concentration of 15% and 5g of sodium silicate, then adjust the pH value to 4 with NaOH, at 90°C every 0.5 hours Add to the reaction kettle, each adding amount is one-third of the total amount, stir and react for 1.5 hours, during which the previous part of the bleaching residue is separated before the new mixture is added, and finally the initial bleaching wax is obtained;
[0018] 2. Put the wax in the initial bleaching section into the reactor, then mix and dissolve 200g of hydrogen peroxide solution with a mass percentage concentration of 25% and 5g of ZJ-CH01 oxygen bleaching stabilizer, adjust the pH value to 8 with NaOH, and set the temperature at 90°C Add to the reactor every 0.5 hours, each addition is one-third of the total amount, stir and react for 1.5 hours, during which the previous part of the bleaching residue is sep...
Embodiment 2
[0022] 1. First add 20kg of defatted montan wax to the reactor, then mix and dissolve 6kg of peracetic acid solution with a mass percentage concentration of 20% and 400g of water-soluble chitosan, and then adjust the pH value to 6 with NaOH. Add to the reactor in 0.4 hours, each adding amount is one-fifth of the total amount, stir and react for 2 hours, during which the previous part of the bleaching residue is separated before adding the mixed solution, and finally the initial bleaching wax is obtained;
[0023] 2. Put the wax in the initial bleaching section into the reactor, then mix and dissolve 6kg of hydrogen peroxide solution with a mass percentage concentration of 30% and 400g of self-made BC-YC01 oxygen bleaching stabilizer, adjust the pH value to 10 with NaOH, and Add to the reaction kettle every 0.4 hours, each addition is one-fifth of the total amount, stir and react at 95°C for 2 hours, during which the previous part of the bleaching residue is separated before the...
Embodiment 3
[0028]1. First add 10kg of degreased montan wax to the reaction kettle, then mix and dissolve 2.5kg of peracetic acid solution with a concentration of 18% by mass and 100g of disodium ethylenediaminetetraacetic acid, then use NaOH to adjust the pH value to 5, and set the temperature at 100°C Next, add the reaction kettle every 0.4 hours, each addition is 1 / 4 of the total amount, stir and react for 1 hour, during which the previous part of the bleaching residue is separated before the new mixture is added, and finally the initial bleaching section wax is obtained;
[0029] 2. Put the wax in the initial bleaching section into the reactor, then mix and dissolve 2.5kg of hydrogen peroxide solution with a mass percentage concentration of 28% and 100g of self-made BC-YC01 oxygen bleaching stabilizer, adjust the pH value to 9 with NaOH, and Add to the reaction kettle every 0.4 hours, each addition is 1 / 4 of the total amount, stir and react at 100°C for 1 hour, during which the previou...
PUM
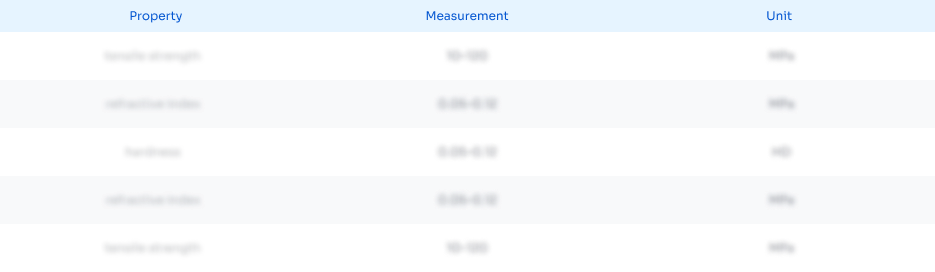
Abstract
Description
Claims
Application Information

- Generate Ideas
- Intellectual Property
- Life Sciences
- Materials
- Tech Scout
- Unparalleled Data Quality
- Higher Quality Content
- 60% Fewer Hallucinations
Browse by: Latest US Patents, China's latest patents, Technical Efficacy Thesaurus, Application Domain, Technology Topic, Popular Technical Reports.
© 2025 PatSnap. All rights reserved.Legal|Privacy policy|Modern Slavery Act Transparency Statement|Sitemap|About US| Contact US: help@patsnap.com