Precise locating method for automatic assembly hole making
A technology of precise positioning and hole position, applied in the direction of manufacturing tools, metal processing machinery parts, measuring/indicating equipment, etc., can solve the problems of reducing the accuracy of hole making, prone to failure, and increasing the time of hole making process, so as to save complex Calculation, the effect of improving machining accuracy
- Summary
- Abstract
- Description
- Claims
- Application Information
AI Technical Summary
Problems solved by technology
Method used
Image
Examples
Embodiment Construction
[0011] Below in conjunction with accompanying drawing and specific embodiment, further illustrate the present invention, should be understood that these embodiments are only for illustrating the present invention and are not intended to limit the scope of the present invention, after having read the present invention, those skilled in the art will understand various aspects of the present invention Modifications in equivalent forms all fall within the scope defined by the appended claims of this application.
[0012] Taking a large aircraft aileron as an example, the specific implementation process of the method of the present invention is described.
[0013] After assembling and positioning the middle rib of the aileron, the pre-connected part of the standard parts forms a stable component to reach the hole-making state, that is, it has a certain rigidity and can be clamped on the assembly frame to meet the non-deformed state during processing of the five-axis machining center...
PUM
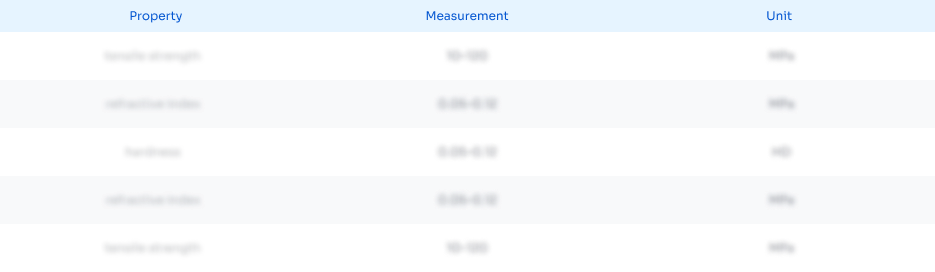
Abstract
Description
Claims
Application Information

- Generate Ideas
- Intellectual Property
- Life Sciences
- Materials
- Tech Scout
- Unparalleled Data Quality
- Higher Quality Content
- 60% Fewer Hallucinations
Browse by: Latest US Patents, China's latest patents, Technical Efficacy Thesaurus, Application Domain, Technology Topic, Popular Technical Reports.
© 2025 PatSnap. All rights reserved.Legal|Privacy policy|Modern Slavery Act Transparency Statement|Sitemap|About US| Contact US: help@patsnap.com