Preparation method of preprocessed clay/rubber nano composite material
A composite material and rubber nanotechnology, which is applied in the field of preparing high-performance and highly dispersed clay/rubber nanocomposites, can solve the problems of clay sheet aggregation, poor interaction, and low grafting amount of silane coupling agent grafted clay, etc. To achieve the effect of simple process
- Summary
- Abstract
- Description
- Claims
- Application Information
AI Technical Summary
Problems solved by technology
Method used
Image
Examples
Embodiment 1
[0039] Add 500 g of commercially available natural sodium-based bentonite into 10 L of deionized water, stir at 800 r / min for 8 hours, and let stand for 24 hours to obtain a clay / water suspension with a solid content of 2.0%. Take 250g of clay / water suspension A, add concentrated hydrochloric acid to make the concentration of HCl 0.02mol / L, and stir and react at 60°C for 3h. Neutralize to pH=7 with sodium carbonate. The temperature was raised to 80° C., 5.0 g of γ-methacryloxypropyltrimethoxysilane was added, and the reaction was stirred for 5 hours to obtain a suspension B. Suspension B was centrifuged at 4000r / min for 20min, and the precipitate was added to 250g of absolute ethanol, stirred at 60°C for 30min at 400r / min to obtain suspension C. Then the suspension C was centrifuged at 4000r / min for 20min, and the sediment was washed twice with absolute ethanol. Then add the sediment obtained by centrifugation into water, stir at room temperature for 30 minutes, and rotate a...
Embodiment 2
[0043] The difference from Example 1 is that 500 g of the clay / water suspension was acid-treated, and 10.0 g of γ-methacryloxypropyltrimethoxysilane was added. Other processes and vulcanization aids were the same as in Example 1. Among them, styrene-butadiene rubber is 100phr, and clay is 10phr. Mix various additives to obtain rubber compound. Vulcanize according to the positive curing time at 170 degrees Celsius to obtain clay / rubber nanocomposites. Tested according to national standards, the mechanical properties of composite materials are shown in Table 1, and the stress-strain curves are shown in figure 1 Curve (c) in .
Embodiment 3
[0045] The difference from Example 2 is that the acid used in the acid treatment is concentrated sulfuric acid, and the clay / water suspension is added to make the hydrogen ion concentration of the system 6 mol / L. Other techniques and vulcanization aids are the same as in Example 1. Among them, styrene-butadiene rubber is 100phr, and clay is 10phr. Mix various additives to obtain rubber compound. Vulcanize according to the positive curing time at 170 degrees Celsius to obtain clay / rubber nanocomposites. Tested according to national standards, the mechanical properties of composite materials are shown in Table 1, and the stress-strain curves are shown in figure 1 Curve (d) in .
[0046] Compared with Comparative Example 2 and Comparative Example 3, the tensile strength, modulus and tear strength of the clay / rubber nanocomposites prepared in Example 2 and Example 3 are all significantly improved.
PUM
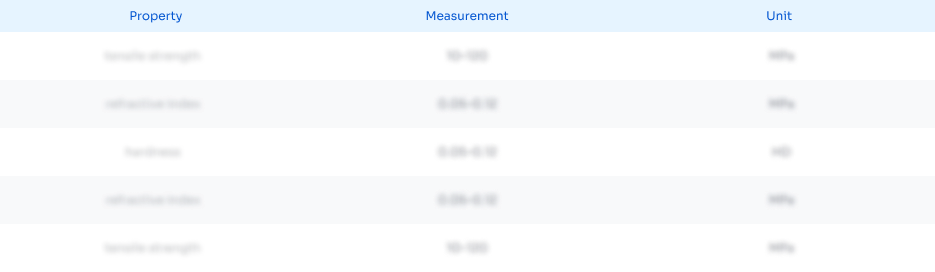
Abstract
Description
Claims
Application Information

- R&D
- Intellectual Property
- Life Sciences
- Materials
- Tech Scout
- Unparalleled Data Quality
- Higher Quality Content
- 60% Fewer Hallucinations
Browse by: Latest US Patents, China's latest patents, Technical Efficacy Thesaurus, Application Domain, Technology Topic, Popular Technical Reports.
© 2025 PatSnap. All rights reserved.Legal|Privacy policy|Modern Slavery Act Transparency Statement|Sitemap|About US| Contact US: help@patsnap.com