Method for producing citrate by using microchannel reactor
A technology of microchannel reactor and citric acid ester, which is applied in chemical instruments and methods, preparation of carboxylic acid esters, preparation of organic compounds, etc., can solve the problems of high energy consumption and heavy pollution, and achieve low energy consumption and low reaction volume The effect of small size and simple process
- Summary
- Abstract
- Description
- Claims
- Application Information
AI Technical Summary
Problems solved by technology
Method used
Image
Examples
Embodiment 1
[0024] Microchannel Reactor 1, see figure 1 , comprising an inlet 2, a catalyst column 3 and an outlet 4 connected in sequence through a connecting pipe, the inlet 2 is connected with a solution tank 6 through a liquid inlet pipe, a solution pump 7 is arranged on the liquid inlet pipe, and a heating sleeve 5 is also included, and the heating Sleeve pipe 5 is sleeved on the catalyst column 3; The pipeline diameter of this microchannel reactor is 2.1mm, and the liquid inlet pipe length is 15cm, and the connecting pipe length between inlet 2 and catalyst column 3 is 25cm, and catalyst column 3 and The length of the connecting pipe between the outlets 4 is 20cm; the volume of the catalyst column is 3mL, and the column is filled with D001 strong acid resin.
[0025] Take 340 g of citric acid monohydrate and 480 g of n-butanol and heat and stir to form a homogeneous phase to obtain a mixed solution; pump the mixed solution into a microchannel reactor. The reaction fluid flowed thro...
Embodiment 2
[0027] Microchannel reactor 1 is basically the same as Example 1, and the difference is only: the pipeline diameter of this microchannel reactor is 2.1mm, and the length of the liquid inlet pipe is 10cm, and the connection between the inlet 2 and the catalyst column 3 The length of the tube is 20cm, and the length of the connecting tube between the catalyst column 3 and the outlet 4 is 30cm; the volume of the catalyst column is 2mL, and the column is filled with solid superacid S 2 o 8 2- / SnO 2 SiO 2 .
[0028] Take 340 g of citric acid monohydrate and 430 g of n-propanol and heat and stir to form a homogeneous phase to obtain a mixed solution; pump the mixed solution into a microchannel reactor. The reaction fluid flowed through the catalyst column at a rate of 0.1 mL / min, and the jacket heating temperature of the catalyst column was 110°C. The crude product is collected at the outlet; the esterification rate is calculated by measuring the acid value. The determination...
Embodiment 3
[0030] Microchannel reactor 1 is basically the same as embodiment 1, and the difference is only: the pipeline of this microchannel reactor is 0.5mm, and the length of the liquid inlet pipe is 30cm, and the connecting pipe between the inlet 2 and the catalyst column 3 The length is 10cm, the length of the connecting pipe between the catalyst column 3 and the outlet 4 is 10cm; the catalyst column is 1mL, and the column is filled with solid superacid S with a mass ratio of 1:1 2 o 8 2- / SnO 2 SiO 2 And D001 strong acid resin.
[0031] Take 1 mol of citric acid monohydrate and 3 mol of ethanol and heat and stir to form a homogeneous phase to obtain a mixed solution; pump the mixed solution into a microchannel reactor. The reaction fluid flowed through the catalyst column at 0.8 mL / min, and the jacket heating temperature of the catalyst column was 100°C. The crude product is collected at the outlet; the esterification rate is calculated by measuring the acid value. The determ...
PUM
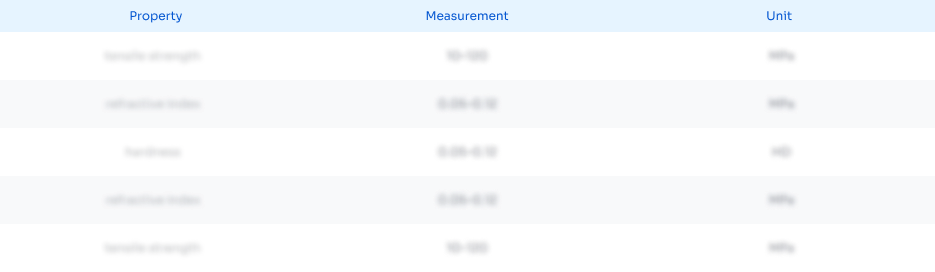
Abstract
Description
Claims
Application Information

- R&D
- Intellectual Property
- Life Sciences
- Materials
- Tech Scout
- Unparalleled Data Quality
- Higher Quality Content
- 60% Fewer Hallucinations
Browse by: Latest US Patents, China's latest patents, Technical Efficacy Thesaurus, Application Domain, Technology Topic, Popular Technical Reports.
© 2025 PatSnap. All rights reserved.Legal|Privacy policy|Modern Slavery Act Transparency Statement|Sitemap|About US| Contact US: help@patsnap.com