Anodic oxidation treatment process of die-casting aluminum alloy for digital electronic product
A technology of anodizing and treatment process, applied in the field of aluminum alloy, can solve the problem of low specific strength, and achieve the effect of inhibiting the deterioration of fatigue performance and ensuring performance
- Summary
- Abstract
- Description
- Claims
- Application Information
AI Technical Summary
Problems solved by technology
Method used
Image
Examples
Embodiment 1-3, and comparative example 1-5
[0016] 1) Raw material preparation: Prepare raw materials according to the alloy composition ratio in Table 1, including pure aluminum with a purity of 99.9%, aluminum-silicon alloy with a silicon content of 12-15%, aluminum-zinc alloy with a zinc content of 10-15%, electrolytic Copper, electrolytic nickel, industrial pure magnesium, industrial pure zirconium, industrial pure titanium and other raw materials.
[0017] 2) Melting: Preheat the above-mentioned raw materials to at least 200°C, then heat the pure aluminum in a melting furnace to 800°C, then add electrolytic copper, electrolytic nickel, commercially pure zirconium and pure titanium, and keep stirring until All the raw materials are melted, then lower the temperature to 720°C and add aluminum-silicon alloy and aluminum-zinc alloy and continue to stir until the raw materials are completely melted, then lower the temperature to 660°C and press industrial pure magnesium to the bottom of the melt for at least 5 minutes, t...
Embodiment 6-7
[0040] Examples 6-7, and Comparative Examples 14-18, the chemical composition of the alloy is the same as that of Example 2, and the optimal selection of the parameters of the electrolyte composition in the two anodic oxidations is mainly investigated. The selection of parameters and performance results are shown in Table 3 , wherein the current density, voltage and oxidation time are the same as in Example 2.
[0041] table 3
[0042]
[0043] In addition to the experiments in Table 3, the conventional CAA method and SAA method were also used to anodize aluminum alloys with the same composition, and the results showed that the fatigue strength could only reach 2×10 4 About the order of magnitude, far less than this application.
[0044] The above results show that the composition of the two-time anodic oxidation has an important influence on the fatigue strength of the alloy. Firstly, the fatigue strength of the two-time anodic oxidation has obvious advantages compared wi...
Embodiment 8-9
[0046] Examples 8-9, and comparative examples 19-22, the chemical composition of the alloy is the same as that of Example 2, and the optimal selection of parameters such as current density, voltage and oxidation time in the two anodic oxidations, the selection of parameters and the performance The results are shown in Table 4, wherein the composition of the electrolyte is the same as in Example 2.
[0047] Table 4
[0048]
[0049] From the results in Table 4, it can be seen that the current density of anodic oxidation should not be too small, otherwise it will make the order of the pores of the oxide film difficult to meet the requirements and become the source of fatigue damage, but the current density should not be too large, otherwise the pores will Excessive pit depth can also become a source of fatigue damage. The oxidation time should not be too short, otherwise it will not meet the basic requirements of anodic oxidation, and it will not be conducive to improving th...
PUM
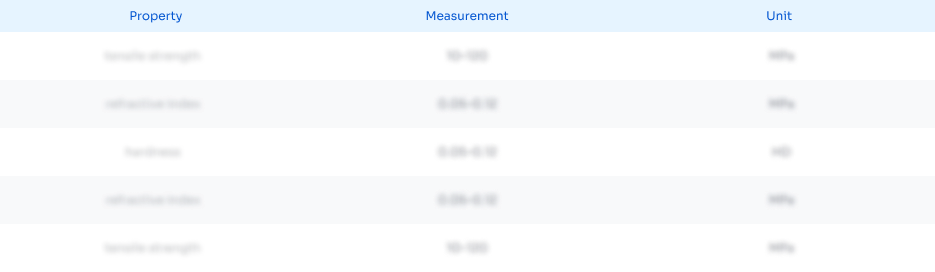
Abstract
Description
Claims
Application Information

- R&D
- Intellectual Property
- Life Sciences
- Materials
- Tech Scout
- Unparalleled Data Quality
- Higher Quality Content
- 60% Fewer Hallucinations
Browse by: Latest US Patents, China's latest patents, Technical Efficacy Thesaurus, Application Domain, Technology Topic, Popular Technical Reports.
© 2025 PatSnap. All rights reserved.Legal|Privacy policy|Modern Slavery Act Transparency Statement|Sitemap|About US| Contact US: help@patsnap.com