Method for forming steel blade in one-time pressing mode
A press forming, steel blade technology, applied in the field of forming components of axial flow fans, can solve problems such as affecting work efficiency, time-consuming and laborious, easy to crack, etc., and achieve shortened processing technology and cycle, reasonable and reliable technology, and low cost Effect
- Summary
- Abstract
- Description
- Claims
- Application Information
AI Technical Summary
Problems solved by technology
Method used
Image
Examples
Embodiment Construction
[0012] The one-time pressing and forming method of the steel blade adopts the following steps: a. Cut the steel plate according to the designed fan blade model and draw a positioning reference line; b. Align and fix the center line of the bending die 1 with the positioning reference line of the steel plate , the bending upper die 2 is pressed down, and pre-bending is carried out at room temperature until the steel plate is bent to 17-23 degrees; c, the curved steel plate 3 is heated in a temperature-controllable resistance furnace, and the temperature range is controlled at 650-850 ° C; d 1. Put the heated curved steel plate 3 into the forming lower die 4, and put the inner core 5 into the curved steel plate 3, the lower end of the forming lower die 4 is fixed with a lower die base 6, and the front end of the forming lower die 4 is fixed with a Locating pin 7; e, press down the front forming upper die 8 and the rear forming upper die 9 that are hinged to each other until the bl...
PUM
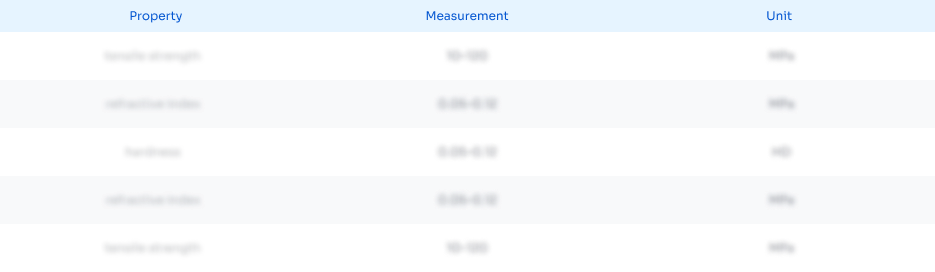
Abstract
Description
Claims
Application Information

- R&D
- Intellectual Property
- Life Sciences
- Materials
- Tech Scout
- Unparalleled Data Quality
- Higher Quality Content
- 60% Fewer Hallucinations
Browse by: Latest US Patents, China's latest patents, Technical Efficacy Thesaurus, Application Domain, Technology Topic, Popular Technical Reports.
© 2025 PatSnap. All rights reserved.Legal|Privacy policy|Modern Slavery Act Transparency Statement|Sitemap|About US| Contact US: help@patsnap.com