Preparation method of double-layer graphene films
A double-layer graphene and thin film technology, applied in graphene, coating, metal material coating process and other directions, can solve the urgent problems of production technology, and achieve the effect of uniform and stable structure, high surface coverage and excellent performance
- Summary
- Abstract
- Description
- Claims
- Application Information
AI Technical Summary
Problems solved by technology
Method used
Image
Examples
Embodiment 1
[0017] Embodiment 1: Utilize copper foil as metal foil, methane gas as carbon source, triethyl borate as cocatalyst, prepare double-layer graphene
[0018] 1) Clean the copper foil with a thickness of 25um in acetone, isopropanol, deionized water, and ethanol for 10 minutes respectively, and dry the surface of the copper foil with nitrogen;
[0019] 2) Spin-coat 120nm-thick triethyl borate (purity of triethyl borate is 97%) on the surface of copper foil, and bake at 50°C for 3 minutes to obtain a combination of triethyl borate and copper foil;
[0020] 3) Place the quartz boat carrying the combination of triethyl borate and copper foil in the reaction chamber of the chemical vapor deposition (CVD) equipment, and evacuate to a pressure of 2×10 -4 Pa; then pass in hydrogen to make the air pressure in the reaction chamber of the equipment reach 170pa, and then raise the temperature in the reaction chamber of the equipment to 1000°C within 40 minutes and keep it for 30 minutes to ...
Embodiment 2
[0023] Embodiment 2: Utilize the copper-nickel alloy foil that contains 3%wt nickel content as metal substrate, acetylene gas as carbon source, the decaborane-anisole mixed solution of 0.04g / ml as cocatalyst, prepare double-layer graphene
[0024] 1) Spin-coat a mixture of decaborane-anisole with a thickness of 60nm and a concentration of 0.04g / ml on the surface of copper-nickel alloy foil, and bake at 60°C for 5 minutes to obtain a mixture of decaborane-anisole Liquid and copper-nickel alloy foil combination;
[0025] 2) Place the quartz boat carrying the decaborane-anisole mixture and the copper-nickel alloy foil combination in the reaction chamber of the chemical vapor deposition (CVD) equipment, and evacuate to a pressure of 2.5×10 -4 Pa; then hydrogen gas is introduced to make the air pressure in the reaction chamber of the equipment reach 300pa, and then the temperature in the reaction chamber of the equipment is raised to 900°C within 50 minutes and kept for 20 minutes ...
Embodiment 3
[0028] Embodiment 3: Utilize 700nm thick copper thin film as metal base, ethanol as carbon source, triethyl borate is cocatalyst, prepares bilayer graphene
[0029] 1) Spray 100nm thick triethyl borate (triethyl borate purity 97%) on the surface of 700nm thick copper film, and bake at 40°C for 2 minutes to obtain a combination of triethyl borate and copper film;
[0030] 2) Place the quartz boat carrying the combination of triethyl borate and copper film in the reaction chamber of the chemical vapor deposition (CVD) equipment, and evacuate to a pressure of 3.2×10 -4 Pa; then feed hydrogen to make the air pressure in the reaction chamber of the equipment reach 600pa, and then raise the temperature in the reaction chamber of the equipment to 850°C for 10 minutes within 35 minutes to remove the oxide layer on the surface of the copper film and make the cocatalyst triethyl borate The ester is fully soluble in the copper film;
[0031] 3) Keep the temperature in the reaction chamb...
PUM
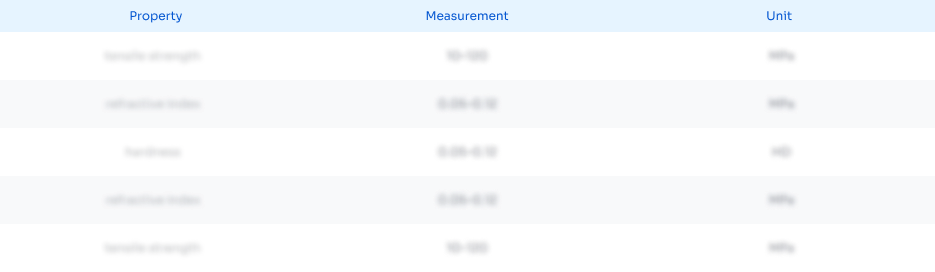
Abstract
Description
Claims
Application Information

- R&D Engineer
- R&D Manager
- IP Professional
- Industry Leading Data Capabilities
- Powerful AI technology
- Patent DNA Extraction
Browse by: Latest US Patents, China's latest patents, Technical Efficacy Thesaurus, Application Domain, Technology Topic, Popular Technical Reports.
© 2024 PatSnap. All rights reserved.Legal|Privacy policy|Modern Slavery Act Transparency Statement|Sitemap|About US| Contact US: help@patsnap.com