Double-surface pressing connecting through hole structure of printed-circuit board and machining method thereof
A technology for printed circuit boards and processing methods, which is applied in the directions of printed circuit components, electrical connection formation of printed components, and electrical connection of printed components, which can solve the problems of increased processing difficulty and high thickness, so as to improve wiring density and eliminate parasitic capacitance , beneficial to the effect of integrity
- Summary
- Abstract
- Description
- Claims
- Application Information
AI Technical Summary
Problems solved by technology
Method used
Image
Examples
Embodiment
[0057] Example: see Figure 13 , according to the above-mentioned processing method, the double-sided press-through hole structure of the printed circuit board includes a circuit board substrate 1 with a thickness of 6.1mm, and a left hole and a right hole are drilled on the circuit board substrate 1; It is the left crimping hole 3 with a diameter of 0.55mm; the middle part is the left non-metallized small hole 5 with a diameter of 0.35mm; both ends of the right hole are right crimping holes 4 with a diameter of 0.55mm; The metallized small hole 6 has a diameter of 0.35 mm, and the surface of the left crimping hole 3 and the right crimping hole 4 has a 25 μm electroplated copper layer 2; the above-mentioned dimensions can be adjusted according to actual needs.
PUM
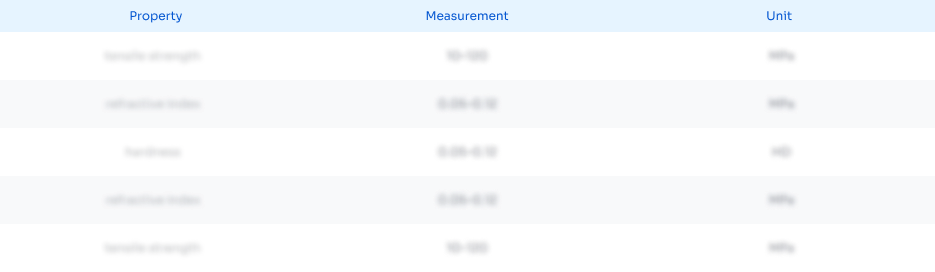
Abstract
Description
Claims
Application Information

- Generate Ideas
- Intellectual Property
- Life Sciences
- Materials
- Tech Scout
- Unparalleled Data Quality
- Higher Quality Content
- 60% Fewer Hallucinations
Browse by: Latest US Patents, China's latest patents, Technical Efficacy Thesaurus, Application Domain, Technology Topic, Popular Technical Reports.
© 2025 PatSnap. All rights reserved.Legal|Privacy policy|Modern Slavery Act Transparency Statement|Sitemap|About US| Contact US: help@patsnap.com