Sol-gel method for preparing zinc-ion-modified carbon-coated lithium vanadium phosphate used as anode material of lithium ion battery
A technology of carbon-coated lithium vanadium phosphate and sol-gel method, which is applied in the field of lithium vanadium phosphate materials and its preparation, can solve the problems of low electronic conductivity and poor cycle performance, and achieve excellent electrochemical performance of the material and optimize the electrochemical performance. Chemical performance and the effect of less reactants
- Summary
- Abstract
- Description
- Claims
- Application Information
AI Technical Summary
Problems solved by technology
Method used
Image
Examples
Embodiment 1
[0024]Dissolve 6.189g of citric acid in 20mL of deionized water, pour it into a beaker containing 2.679g of vanadium pentoxide, and stir on a magnetic heating stirrer at a constant temperature of 60°C for 30 minutes to form a dark blue solution. Dissolve 5.080 g of ammonium dihydrogen phosphate and 1.632 g of lithium carbonate in 20 mL of deionized water, respectively, and add them to the dark blue solution. At this time, the pH value of the solution was 7, and the mixed liquid was stirred at a constant temperature of 60° C. for 1.5 hours on a magnetic heating stirrer. Raise the temperature to 80°C, stir to evaporate the solvent to form a dark blue wet gel, put it in an oven at 80°C and let it stand for 1 day to form a dry gel. Grinding the xerogel with a mortar for 30 minutes turned into a green powder. Incubate at 350°C for 4 hours under a hydrogen-nitrogen mixture containing 5% (volume ratio) of hydrogen to remove gases such as ammonia and water vapor. Then heat up to 750...
Embodiment 2
[0027] Dissolve 5.156g of citric acid in 20mL of deionized water, pour it into a beaker containing 2.219 vanadium pentoxide, and stir on a magnetic heating stirrer at a constant temperature of 60°C for 30 minutes to form a dark blue solution. Dissolve 4.232g of ammonium dihydrogen phosphate, 1.360g of lithium carbonate and 0.011g of zinc oxide in 20mL of deionized water respectively, add to the dark blue solution, and stir for 30 minutes at a constant temperature of 60°C on a magnetic heating stirrer. The pH value was adjusted to 4 with acetic acid, and the mixed liquid was stirred at a constant temperature of 60° C. for 1 hour on a magnetic heating stirrer. Raise the temperature to 80°C, stir to evaporate the solvent to form a dark blue wet gel, put it in an oven at 80°C and let it stand for 1 day to form a dry gel. Grinding the xerogel with a mortar for 30 minutes turned into a green powder. Incubate at 350°C for 4 hours under a hydrogen-nitrogen mixture containing 5% (volu...
Embodiment 3
[0030] Dissolve 5.154g of citric acid in 20mL of deionized water, pour it into a beaker containing 2.208g of vanadium pentoxide, and stir on a magnetic heating stirrer at a constant temperature of 60°C for 30 minutes to form a dark blue solution. Dissolve 4.231g of ammonium dihydrogen phosphate, 1.360g of lithium carbonate and 0.021g of zinc oxide in 20mL of deionized water respectively, add to the dark blue solution, and stir for 30 minutes at a constant temperature of 60°C on a magnetic heating stirrer. The pH value was adjusted to 4 with acetic acid, and the mixed liquid was stirred at a constant temperature of 60° C. for 1 hour on a magnetic heating stirrer. Raise the temperature to 80°C, stir to evaporate the solvent to form a dark blue wet gel, put it in an oven at 80°C and let it stand for 1 day to form a dry gel. Grinding the xerogel with a mortar for 30 minutes turned into a green powder. Incubate at 350°C for 4 hours under a hydrogen-nitrogen mixture containing 5% (...
PUM
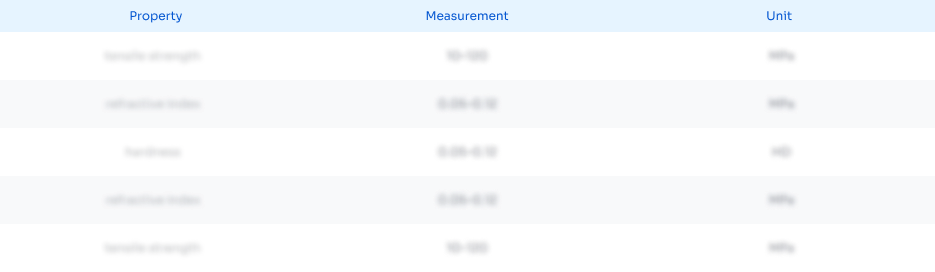
Abstract
Description
Claims
Application Information

- R&D Engineer
- R&D Manager
- IP Professional
- Industry Leading Data Capabilities
- Powerful AI technology
- Patent DNA Extraction
Browse by: Latest US Patents, China's latest patents, Technical Efficacy Thesaurus, Application Domain, Technology Topic, Popular Technical Reports.
© 2024 PatSnap. All rights reserved.Legal|Privacy policy|Modern Slavery Act Transparency Statement|Sitemap|About US| Contact US: help@patsnap.com