Motor control method based on PI parameter self-tuning
A parameter self-tuning and motor control technology, applied in the direction of motor generator control, electronic commutation motor control, control system, etc., can solve the problems of system overshoot or oscillation, single research, precision drop, etc., to achieve strong self-adaptation, Strong anti-interference ability
- Summary
- Abstract
- Description
- Claims
- Application Information
AI Technical Summary
Problems solved by technology
Method used
Image
Examples
Embodiment Construction
[0017] Specific embodiments of the present invention will be described in detail below in conjunction with the accompanying drawings, so that those skilled in the art can better understand the present invention.
[0018] Such as figure 1 , 2 Shown is a specific implementation of the motor control method based on PI parameter self-tuning of the present invention, and its specific implementation steps are:
[0019] (1) if figure 1 As shown, the three-phase current i of the motor (permanent magnet synchronous motor) 1 is collected through the Hall sensor a i b i c , and then through Clarke transformation 3 and Park transformation 4 to get the actual current value i of the motor in the d-q coordinate system d i q ;
[0020] (2) Collect the position signal of the motor 1 through the position signal detector 2, and differentiate the position signal to obtain the speed signal;
[0021] (3) The genetic controller 5 is used to optimize the fuzzy control rules, quantization fact...
PUM
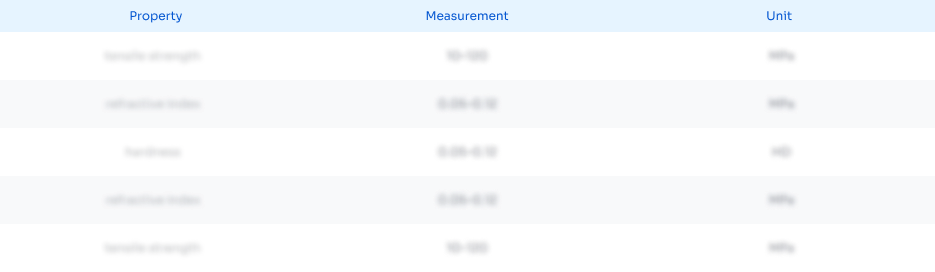
Abstract
Description
Claims
Application Information

- R&D
- Intellectual Property
- Life Sciences
- Materials
- Tech Scout
- Unparalleled Data Quality
- Higher Quality Content
- 60% Fewer Hallucinations
Browse by: Latest US Patents, China's latest patents, Technical Efficacy Thesaurus, Application Domain, Technology Topic, Popular Technical Reports.
© 2025 PatSnap. All rights reserved.Legal|Privacy policy|Modern Slavery Act Transparency Statement|Sitemap|About US| Contact US: help@patsnap.com