Chromium, nickel alloy and method for producing high-temperature dust-corrosion-resistant furnace tube by centrifugal casting of the alloy
A technology of centrifugal casting and nickel alloy, which is applied in the direction of boiler water pipes, boiler smoke pipes/fire pipes, components of steam boilers, etc., can solve the problems of long delivery period, high production cost, expensive price, etc., and overcome the problem of poor fluidity Poor, low cost, simple method effect
- Summary
- Abstract
- Description
- Claims
- Application Information
AI Technical Summary
Problems solved by technology
Method used
Examples
Embodiment
[0008] The chromium and nickel alloy of the present embodiment and the method for centrifugally casting the alloy to produce a furnace tube resistant to high-temperature dusting and corrosion, the chemical components of the chromium and nickel alloy are as follows: Si: 0.3%-0.5%, Mn: 0.3%-0.5 %, P≤0.02%, S≤0.01%, Cr: 24%-26%, Ni: 59.3%-65.5%, Mo≤0.5%, Cu: 0.03%-0.05%, Al: 1.8%-2.4%, remainder The amount is the microalloying elements Ti, Zr, Re. The method of producing high-temperature dust corrosion-resistant furnace tubes by centrifugal casting of chromium and nickel alloys includes alloy smelting and centrifugal casting. The specific steps are as follows: (1) alloy smelting, melting ferrochrome in an electric furnace, and then adding nickel plate and ferromolybdenum , ferrosilicon, ferromanganese, and copper alloys, control the carbon content to meet the requirements, adjust the composition before the furnace to meet the requirements, raise the melt temperature to 1600°C, ad...
PUM
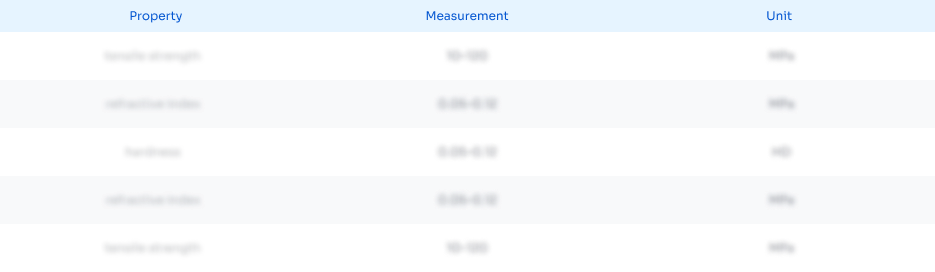
Abstract
Description
Claims
Application Information

- R&D Engineer
- R&D Manager
- IP Professional
- Industry Leading Data Capabilities
- Powerful AI technology
- Patent DNA Extraction
Browse by: Latest US Patents, China's latest patents, Technical Efficacy Thesaurus, Application Domain, Technology Topic, Popular Technical Reports.
© 2024 PatSnap. All rights reserved.Legal|Privacy policy|Modern Slavery Act Transparency Statement|Sitemap|About US| Contact US: help@patsnap.com