Noncorrosive water-based cutting fluid
A non-corrosive, cutting fluid technology, applied in the petroleum industry, lubricating compositions, etc., can solve the problems of poor biodegradability, short service life, and large environmental pollution
- Summary
- Abstract
- Description
- Claims
- Application Information
AI Technical Summary
Problems solved by technology
Method used
Image
Examples
Embodiment 1
[0041] Put 20 parts of sebacic acid, 9 parts of undecanedibasic acid and 15 parts of triethanolamine together, react at a high temperature of 120°C for 60 minutes, and cool down to 60°C to obtain a rust inhibitor.
[0042] The above rust inhibitor, 5 parts of borate, 2 parts of polyethylene glycol 400, 3 parts of monoethanolamine, 2 parts of diethanolamine, 5 parts of protective agent saponified glycerin, 0.5 part of sodium hydroxide, 0.1 part of sodium carbonate, softener 0.5 part of tetrasodium EDTA, 0.1 part of non-ionic surfactant OP-10 degreasing agent, 1 part of disinfectant Cathone, 0.5 part of sodium benzoate, 0.5 part of di-tert-butyl p-cresol, copper corrosion inhibitor benzotriazepam Put 1 part of azole and 0.1 part of film-coating agent polyalkyl acrylate together, heat to 120 ° C, react for 1 hour, stop standing for more than 6 hours, filter to make mother liquor, and finally add 34.7 parts of water to make non-corrosive water-based cutting liquid.
[0043] The p...
Embodiment 2
[0045] Put 10 parts of sebacic acid, 3 parts of undecanedibasic acid and 5 parts of triethanolamine together, react at a high temperature of 100°C for 60 minutes, and cool down to 60°C to obtain a rust inhibitor.
[0046] The above rust inhibitor, 15 parts of borate, 3 parts of polyethylene glycol 400, 9 parts of monoethanolamine, 6 parts of diethanolamine, 15 parts of protective agent saponified glycerin, 1 part of sodium hydroxide, 1 part of sodium carbonate, softener 2 parts of tetrasodium EDTA, 1 part of non-ionic surfactant OP-10 degreasing agent, 1 part of disinfectant Cathone, 0.5 parts of sodium benzoate, 2 parts of di-tert-butyl p-cresol, copper corrosion inhibitor benzotriazepam Put 5 parts of azole and 1 part of film-coating agent polyalkyl acrylate together, heat to 100°C, react for 1 hour, stop standing still for more than 6 hours, filter to make mother liquor, and finally add 19.5 parts of water to make non-corrosive water-based cutting liquid.
Embodiment 3
[0048] Put 15 parts of sebacic acid, 6 parts of undecanedibasic acid and 10 parts of triethanolamine together, react at a high temperature of 110°C for 60 minutes, and cool down to 60°C to obtain a rust inhibitor.
[0049] The above antirust agent, 10 parts of borate, 2.5 parts of polyethylene glycol 400, 6 parts of monoethanolamine, 4 parts of diethanolamine, 10 parts of protective agent saponified glycerin, 0.7 part of sodium hydroxide, 0.6 part of sodium carbonate, softener 1.2 parts of tetrasodium EDTA, 0.5 parts of non-ionic surfactant OP-10 degreasing agent, 1 part of disinfectant Cathone, 0.5 parts of sodium benzoate, 1 part of di-tert-butyl p-cresol, copper corrosion inhibitor benzotriazepam Put 3 parts of azole and 0.5 part of polyalkyl acrylate as the coating agent together, heat to 110°C, react for 1 hour, stop standing for more than 6 hours, filter to make mother liquor, and finally add 27.5 parts of water to make non-corrosive water-based cutting liquid.
PUM
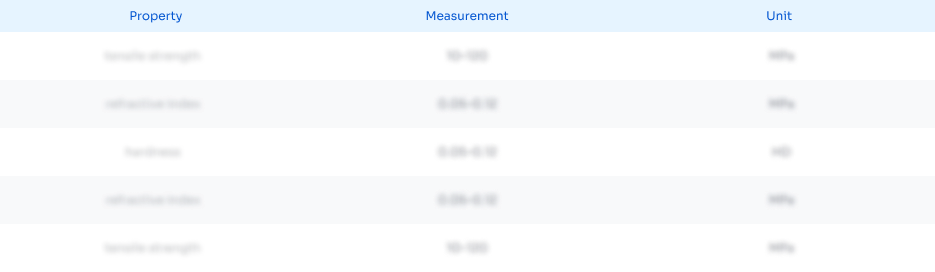
Abstract
Description
Claims
Application Information

- R&D Engineer
- R&D Manager
- IP Professional
- Industry Leading Data Capabilities
- Powerful AI technology
- Patent DNA Extraction
Browse by: Latest US Patents, China's latest patents, Technical Efficacy Thesaurus, Application Domain, Technology Topic, Popular Technical Reports.
© 2024 PatSnap. All rights reserved.Legal|Privacy policy|Modern Slavery Act Transparency Statement|Sitemap|About US| Contact US: help@patsnap.com