Pressure-controlled friction stir welding main shaft head device
A friction stir welding and pressure control technology, applied in welding equipment, manufacturing tools, non-electric welding equipment, etc., can solve the problems of complex structure and control mechanism of FSW equipment, and achieve easy control, simple hydraulic system, simple and compact structure Effect
- Summary
- Abstract
- Description
- Claims
- Application Information
AI Technical Summary
Problems solved by technology
Method used
Image
Examples
Embodiment
[0042] To manufacture a certain friction stir welding equipment that meets the welding pressure controllable welding, the welding speed range is 100-3000rpm, the welding pressure range is 5-60kN, and a special spindle head is now designed for it. The spindle head can be used as figure 1 The structure shown, its design steps are as follows:
[0043] Bearings are selected according to the spindle speed and axial load requirements: while the spindle rotates at high speed, its axial load capacity must be guaranteed, and angular contact spindle bearings are usually selected; the contact angle of this type of bearing is generally 15° or 25°; In some cases, in order to improve the axial bearing capacity of the main shaft, multiple bearings can be assembled in series; it is recommended that three angular contact bearings with a contact angle of 25° be selected for the bearing group at the front end of the main shaft and arranged in series with TTL.
[0044] Design the size of the sha...
PUM
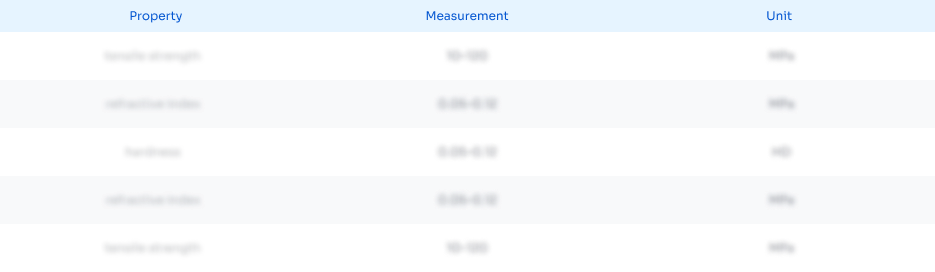
Abstract
Description
Claims
Application Information

- R&D Engineer
- R&D Manager
- IP Professional
- Industry Leading Data Capabilities
- Powerful AI technology
- Patent DNA Extraction
Browse by: Latest US Patents, China's latest patents, Technical Efficacy Thesaurus, Application Domain, Technology Topic, Popular Technical Reports.
© 2024 PatSnap. All rights reserved.Legal|Privacy policy|Modern Slavery Act Transparency Statement|Sitemap|About US| Contact US: help@patsnap.com